Données industrielles
Matières premières
Les teneurs de l’écorce terrestre sont de 0,005 ppm, soit 5 µg/kg, pour le platine, 0,015 ppm pour le palladium, 0,0015 ppm pour l’osmium, 0,001 ppm pour le rhodium, l’iridium et le ruthénium.
Les gisements de platinoïdes se trouvent généralement dans des roches magmatiques qui sont remontées en surface au travers de la croûte terrestre. C’est le cas du principal gisement mondial, celui du complexe du Bushveld, en Afrique du Sud, mais aussi de ceux de Great Dyke, au Zimbabwe, de Stillwater, aux États-Unis, de Norilsk en Russie. Dans ces gisements, les platinoïdes sont associés à des sulfures de nickel et de cuivre.
La teneur en platinoïdes des minerais d’Afrique du Sud est comprise entre 3 et 10 g/t. Aux États-Unis, cette teneur est, en moyenne, de 15 g/t. En Russie, dans le gisement de Norilsk-Talnakh, les teneurs varient entre 8 et 11 g/t pour les platinoïdes présents avec les sulfures massifs de nickel ou de cuivre et 3 et 9 g/t pour les platinoïdes présents dans les sulfures disséminés. Pour récupérer une once (31,1035 g) de platinoïdes, il faut extraire de 8 à 16 t de minerai.
En Afrique du Sud et aux États-Unis, les gisements sont exploités pour les platinoïdes contenus, le nickel et le cuivre étant coproduits. A Norilsk, en Russie, et à Sudbury, au Canada, les platinoïdes sont coproduits de mines de nickel.
Il existe une faible production alluviale, sous forme de platine natif, en Colombie et en Russie.
Les exploitations minières sont le plus souvent souterraines.
Productions minières
Production minière de platine
En tonnes de platine contenu, en 2024, sur un total mondial de 178 t. Source : Johnson Matthey
en tonnes de métal contenu
Afrique du Sud |
127,9 t |
|
Zimbabwe |
15,8 t |
Russie |
20,2 t |
|
Canada, États-Unis |
8,3 t |
Source : Johnson Matthey
La production de l’Union européenne, en 2023, en Finlande, est de 953 kg.
Production minière de palladium
En tonnes de palladium contenu, en 2024, sur un total mondial de 206,9 t. Source : Johnson Matthey
en tonnes de métal contenu
Russie |
85,5 t |
|
Canada, États-Unis |
25,3 t |
Afrique du Sud |
75,3 t |
|
Zimbabwe |
13,0 t |
Source : Johnson Matthey
La production de l’Union européenne, en 2023, en Finlande, est de 762 kg.
Production minière de rhodium
En 2024 : monde : 22,2 t.
en tonnes de métal contenu
Afrique du Sud |
18,2 t |
|
Zimbabwe |
1,4 t |
Russie |
1,8 t |
|
Canada, États-Unis |
0,6 t |
Source : Johnson Matthey
Production minière des autres platinoïdes
Ruthénium : environ 40 t/an, à 89,8 % en Afrique du Sud, 4,5 % au Zimbabwe, 4,2 % en Russie et 1,4 % au Canada. En 2024, la production a été de 34,6 t.
Iridium : environ 9 t/an, à 80,9 % en Afrique du Sud, 9,0 % en Russie, 7,4 % au Zimbabwe, 2,6 % au Canada. En 2024, la production a été de 6,9 t.
Osmium: environ 1 t/an.
En Afrique du Sud, l’énorme gisement du Bushveld (voir ci-dessous), découvert en 1924 par Hans Merensky, s’étend sur une surface de 66 000 km2 et une profondeur d’environ 15 km. Il s’est formé pendant 1 à 5 millions d’années, il y a 2 053 millions d’années, par l’intrusion d’un magma basique au travers de la croûte terrestre. Lors de son refroidissement, les minéraux de composition et de température de solidification différentes se sont déposés par cristallisation fractionnée en couches homogènes. Le gisement affleure selon trois lobes :
- à l’ouest, selon un arc de 300 km de long, de Pretoria à Thabazimbi, en passant par Rustenburg,
- à l’est, sur 100 km de long, au nord-est de Middleburg,
- au nord, sur 100 km au nord de Mokopane.
Carte géologique du complexe du Bushveld (Source : Minéralinfo)
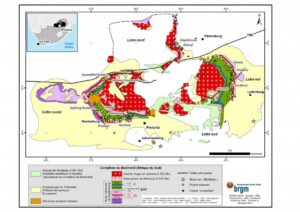
Les platinoïdes se trouvent dans 3 couches, dénommées reefs, à environ 2 000 m de profondeur : Merensky Reef d’une épaisseur moyenne de 30 cm, Upper Group 2 (UG-2) d’une épaisseur comprise entre 0,4 et 2,5 m, située de 20 à 400 m sous Merensky Reef, et Platreef. Aux débuts de leur exploitation, les gisements ont été exploités à faible profondeur, c’est le cas actuellement pour Platreef, mais comme les veines de minerais plongent de 10° vers le centre du complexe du Bushveld, l’exploitation est de plus en plus profonde. Par ailleurs, la faible épaisseur des veines de minerai ne permet pas une mécanisation importante et rend difficile les conditions de travail.
Merensky Reef, est constituée d’environ 60 % d’enstatite (pyroxène) et 20 % de plagioclase (feldspath). Les platinoïdes sont associés à des sulfures constitués de pyrrhotite (sulfure de fer) pour 40 %, pentlandite (sulfure de fer et de nickel) pour 30 %, chalcopyrite (sulfure de fer et de cuivre) pour 15 %. Les platinoïdes, sont présents sous forme de coopérite (PtS), braggite ((Pt,Pd)NiS), pserrylite (PtAs2), laurite (RuS2)… dans des particules d’environ 15 micromètres. Le niveau UG-2 est constitué par 60 à 90 % de chromite (oxyde de fer et de chrome) et de silicates dont 5 à 30 % de pyroxène et 1 à 10 % de plagioclase.
En 2020, 64 % de la production provient du niveau UG2, 21 % de Merensky reef et 15 % de Platreef.
Évolution de la teneur moyenne en Pt, Pd, Rh et Au des minerais extraits : 4,8 g/t en 2000, 3,5 g/t en 2013, 3,35 g/t en 2019.
Le gisement, outre les platinoïdes, contient du cuivre, du nickel, du cobalt, du chrome, du vanadium, du titane, de l’étain, de l’or, de l’argent… Il renferme 80 % des réserves mondiales de chrome, de 40 à 50 % de celles de vanadium.
Teneurs en platinoïdes et en or des reefs sud-africains :
en g/t
Reefs |
Pt |
|
Pd |
|
Rh |
|
Ru |
|
Ir |
|
Os |
|
Au |
Merensky |
3,25 |
|
1,38 |
|
0,17 |
|
0,44 |
|
0,06 |
|
0,04 |
|
0,18 |
UG-2 |
2,46 |
|
2,04 |
|
0,54 |
|
0,72 |
|
0,11 |
|
0,10 |
|
0,02 |
Platreef |
1,26 |
|
1,38 |
|
0,09 |
|
0,12 |
|
0,02 |
|
0,02 |
|
0,10 |
Source : DERA
En Russie, les platinoïdes sont principalement coproduits par Nornickel, ex-Norilsk, dans les mines de nickel des péninsules de Taimyr et de Kola. Les proportions des différents platinoïdes et de l’or sont les suivantes : 17,7 % de Pt, 74,0 % de Pd, 2,0 % de Rh, 1,1 % de Ru, 0,7 % de Ir et 4,5 % de Au. Il existe dans ce pays une production alluviale, en 2018, de 622 kg de platine natif, avec les gisements de Kondyor, près de Khabarovsk, en Sibérie Orientale, exploités par Russian Platinium, où a été trouvé une pépite de 3,5 kg, et de Koryak, dans le Kamchatka.
Au Zimbabwe, les mines de platinoïdes exploitent l’intrusion magmatique du Great Dyke. Anglo American Platinum possède la mine d’Unki et Impala Platinum possède les mines de Zimplats, à 87 % et Mimosa, à 50 %, en joint venture avec Sibanye Stillwater. Les proportions des différents platinoïdes et de l’or sont les suivantes : 45,5 % de Pt, 36,0 % de Pd, 3,9 % de Rh, 4,9 % de Ru, 2,4 % de Ir et 7,2 % de Au.
Au Canada, des platinoïdes sont extraits d’une part de la mine du Lac des Îles, dans l’Ontario et d’autre part sont coproduits dans les mines de nickel de Sudbury, dans l’Ontario, et de Raglan, au nord du Québec.
Le gisement du Lac des Îles qui s’étend sur 1 x 0,815 km et 650 m de profondeur est exploité par Impala Platinum qui l’a acquis, en décembre 2019, auprès de North American Palladium. Le gisement est exploité à ciel ouvert depuis 1993 et souterrainement, depuis 2006. En 2023-24, la production a été de 591 kg de Pt, 7,53 t de Pd ainsi que de l’or, du nickel, du cuivre, de l’argent et du cobalt. Les réserves prouvées et probables sont de 8,5 millions de t de minerai contenant 3,48 g/t de platinoïdes, 0,06 % de nickel et 0,07 % de cuivre.
Les mines de Sudbury, exploitées par Vale, principalement pour le nickel contenu, ont donné, en 2024, 3,33 t de platine, 3,73 t de palladium, 1,18 t d’or et de l’argent ainsi que 58 600 t de cuivre, 36 200 t de nickel et 331 t de cobalt. Les platinoïdes sont concentrés à Port Colborne, dans l’Ontario et raffinés, jusqu’en 2018, à Acton, au Royaume Uni. Cette raffinerie ayant fermé en 2018, les concentrés sont depuis traités par une tierce partie. Les réserves prouvées et probables sont de 64,5 millions de t renfermant 1,34 % de Cu, 1,42 % de Ni, 0,04 % de Co, 0,83 g/t de Pt, 0,98 g/t de Pd et 0,31 g/t de Au.
Glencore exploite des platinoïdes dans la mine de Nickel Rim South, à Sudbury et dans celle de Raglan, avec, en 2024, une production de 776 kg de Pt, 2,177 t de Pd, 93 kg de Rh, 311 kg d’or, 5,4 t de Ag ainsi que 43 000 t de Ni, 13 600 t de Cu et 600 t de Co. Les concentrés de nickel et de cuivre sont raffinés en Norvège, à Kristiansand. Les réserves prouvées et probables sont de 31,3 millions de t renfermant 2,13 % de Ni, 0,81 % de Cu, 0,05 % de Co, 0,55 g/t de Pt et 1,1 g/t de Pd.
Aux États-Unis, la production est assurée par Sibanye Stillwater, après l’acquisition, en mai 2017, des mines souterraines de Stillwater et East Boulder qui exploitent la couche géologique dénommée J-M Reef, dans le sud du Montana, près de la ville de Nye. La teneur moyenne du minerai extrait est, en 2023, de 11,37 g de platinoïdes par t de minerai. En 2024, la production des deux mines a été de 3,010 t de platine et 10,236 t de palladium avec 8,190 t de platine et palladium pour la mine de Stillwater et 5,058 t de platine et palladium pour celle de East Boulder. Les réserves prouvées et probables sont, fin décembre 2024, de 44,5 millions de t de minerai avec une teneur moyenne en platinoïdes de 13,3 g/t de Pt, Pd. Les opérations métallurgiques sont effectuées à Colombus dans le Montana. Les proportions entre les différents platinoïdes sont les suivantes : 22 % de Pt, 78 % de Pd.
Dans l’Union européenne, il y a une faible production de platine et de palladium associée à l’exploitation des gisements polonais de cuivre avec environ 15 kg/an de Pt et 25 kg/an de Pd et surtout l’exploitation à ciel ouvert de la mine de Kevitsa, depuis 2012, dans le nord de la Finlande, le gisement ayant été découvert en 1987. En juin 2016, First Quantum a vendu la mine à Boliden. En 2024, les productions ont été de 26 000 t de Cu, 12 000 t de Ni, 583 t de Co, 431 kg de Au, 958 kg de Pt, 723 kg de Pd. Les réserves prouvées et probables sont de 97,5 millions de t renfermant 0,31 % de Cu, 0,22 % de Ni, 0,010 % de Co, 0,19 g/t de Pt, 0,12 g/t de Pd, 0,10 g/t d’Au.
Minéralurgie : les minerais extraits, sulfurés, sont broyés puis concentrés par flottation dans des installations proches de la mine qui donnent des concentrés sulfurés de nickel et de cuivre renfermant les platinoïdes. Par exemple, en 2016, les mines de Stillwater aux États-Unis ont produit 32 097 t de concentrés renfermant 129 g/t de platine et 439 g/t de palladium, à partir de 1,29 million de t de minerai extrait de la mine contenant 14,0 g/t de platinoïdes. La masse de concentrés produits représente 2,5 % de la masse totale du minerai extrait. Le taux de récupération des platinoïdes est, en 2021, de 89,71 %.
Historique de la production minière : d’après J.F. Labbé, J.J. Dupuy, « Panorama 2012 du marché des platinoïdes« .
Le platine était connu des civilisations égyptiennes et précolombiennes mais son exploitation industrielle a débuté en 1735, en Colombie par l’exploitation de placers et s’est poursuivie, à compter de 1819, dans l’Oural, en Russie. Cette exploitation, exclusivement dans des placers, a donné 281 t entre 1735 et 1918.
En 1919, a commencé l’exploitation minière des platinoïdes contenus dans le gisement de nickel de Sudbury, au Canada, puis, à compter de 1928, celle du reef Merensky, en Afrique du Sud. Au total, entre 1919 et 1946, la production mondiale a été de 280 t.
En 1947, a débuté l’exploitation minière des platinoïdes du gisement de nickel et de cuivre de Norilsk, en Russie et en 1982, celle du reef UG-2 en Afrique du Sud. Au total, entre 1947 et 1994, la production totale a été de 6 632 t.
Entre 1995 et 2017, la production de platinoïdes a été de 9 890 t, soit, depuis 1735, un total de 17 080 t.
Principaux producteurs miniers :
en tonnes de production minière
|
Pt |
|
Pd |
|
Rh |
Impala Platinum, en 2023-24 |
49,455 |
|
36,018 |
|
5,910 |
Sibanye Stillwater, en 2024 |
36,912 |
|
27,302 |
|
5,152 |
Anglo American Platinum, en 2024 |
31,026 |
|
24,842 |
|
3,801 |
Nornickel, en 2024 |
20,746 |
|
85,908 |
|
2,022 |
Northam Platinum, en 2023-24 |
16,367 |
|
8,279 |
|
2,801 |
Vale, en 2024 |
3,330 |
|
3,730 |
|
|
ARM, en 2023-24 |
4,186 |
|
3,135 |
|
0,718 |
Glencore, en 2024 |
0,776 |
|
2,177 |
|
0,093 |
Sources : rapports des sociétés
Voir ci-dessous pour plus de détails.
Réserves minières : en 2024. Monde : plus de 81 000 t.
en t de platinoïdes
Afrique du Sud |
63 000 |
|
États-Unis |
820 |
Russie |
16 000 |
|
Canada |
310 |
Zimbabwe |
1 200 |
|
|
|
Source : USGS
En Afrique du Sud, 71 % des réserves sont situées dans le lobe ouest du complexe du Bushveld, 24 % dans le lobe est et 5 % dans le Platreef. 57 % des réserves sont situées dans le reef Merensky, 38 % dans UG-2, 5 % dans Platreef.
Métallurgie
Les concentrés provenant des exploitations minières subissent une succession de traitements. Exemple des opérations effectuées par Stillwater Mining Co. (SMC) sur les concentrés américains du Montana auxquels ont été ajouté le platine issu du recyclage.
Une série de fusions, à plus de 1 500°C, dans des fours électriques, permet d’éliminer la silice sous forme d’un laitier fusible ainsi qu’une grande partie du fer contenu. On obtient des mattes sous forme de granulés qui contiennent sous forme de sulfures, du cuivre, du nickel, du cobalt et les platinoïdes.
Les mattes sont ensuite traitées selon le procédé Sherritt qui consiste à pratiquer des lixiviations à l’acide sulfurique, en présence de dioxygène. Une première étape à la pression atmosphérique et à chaud permet d’éliminer une grande partie du nickel et du cobalt qui sont récupérés sous forme de sulfates. Une deuxième étape, sous pression et plus haute température dans des autoclaves, fait passer une grande partie du cuivre en solution. Il est récupéré par électrolyse donnant des cathodes de cuivre. Une troisième étape, sous pression et haute température, permet l’élimination du cuivre et du nickel restant.
Les platinoïdes qui sont restés inattaqués lors des traitements de lixiviation se retrouvent dans les « gâteaux » issus des filtres-presses. L’or et l’argent, présents en faible quantité, accompagnent les platinoïdes. La teneur en platinoïdes est passée de 2 % dans les mattes, à 40 % dans les « gâteaux ».
Les opérations de séparation des éléments contenus sont réalisées à l’extérieur de la société pour fournir des éponges titrant 99,95 %. Ces opérations hydrométallurgiques consistent en une attaque par l’acide chlorhydrique en présence de dichlore qui permet de solubiliser l’or puis le palladium et ensuite le platine. Les autres platinoïdes restent insolubles. Les traitements de séparation mis en œuvre font appel à des extractions par solvant, des distillations, des échanges d’ions.
Les concentrés miniers produits par Anglo American Platinum sont traités dans 4 complexes métallurgiques, à Mortimer, Waterval (Rustenburg) et Polokwane, en Afrique et Sud et Unki au Zimbabwe. En 2012, 1,15 million de t de concentrés ont donné 185 100 t de mattes qui après conversion ont fourni 29 600 t de métaux de base (cuivre, nickel et cobalt) et 55 200 t de mattes converties qui après raffinage ont donné 144 t de platinoïdes.
Principaux producteurs :
- Anglo American Platinum (Amplats) dénommé Valterra Platinium depuis mai 2025, avec, en 2024, un total de raffinage de 57 408 t de Pt, 38,833 t de Pd, 7,726 t de Rh, 17,844 t pour les autres platinoïdes et or et 21 800 t de Ni dont avec le raffinage de sa propre production minière de 31,026 t de platine, 24,842 t de palladium, 3,801 t de rhodium, 5,393 t pour les autres platinoïdes et l’or ainsi que, en 2024, 950 000 t de chromite, 26 000 t de nickel et 17 000 t de cuivre. 24,26 millions de t de minerai renfermant 3,2 g/t de platine, palladium, rhodium et or ont été traitées. La répartition des revenus du groupe sont, en 2024, par métaux, de 19,3 % pour le rhodium, 21,3 % pour le palladium, 21,8 % pour le platine, 16,9 % pour les autres platinoïdes et l’or, 7,4 % pour Ni, 3,7 % pour Cr, 1,1 % pour les autres métaux.
Le groupe exploite, en Afrique du Sud, le complexe du Bushveld avec, en propre :
- la mine de Mogalakwena à ciel ouvert, avec, en 2024, une production de 12,706 t de Pt, 13,607 t de Pd, 0,815 t de Rh et en 2023, 0,855 t de Ru, 0,217 t de Ir, 1,580 t d’or, 16 832 t de Ni et 10 729 t de Cu,
- celle d’Amandebult souterraine regroupant les mines de Dishaba et Tumela, avec 9,157 t de Pt, 4,221 t de Pd, 1,645 t de Rh et, en 2023, 2,557 t de Ru, 0,650 t de Ir, 0,084 t d’or, 918 000 t de chromite, 749 t de Ni et 294 t de Cu,
- celle de Mototolo, détenue entièrement après l’achat en novembre 2018, des parts de Glencore avec, 3,913 t de Pt, 2,647 t de Pd, 0,718 t de Rh et, en 2023, 1,191 t de Ru, 0,274 t de Ir, 0,072 t d’or, 532 t de Ni et 221 t de Cu,
- le groupe exploite également la mine d’Unki, au Zimbabwe qui a produit, en 2024, 3,393 t de Pt, 2,877 t de Pd, 0,330 t de Rh et, en 2023, 0,333 t de Ru, 0,140 t de Ir, 0,423 t d’or, 3 603 t de Ni et 2 976 t de Cu.
Exploite également en association le complexe minier de Modikwa, partagé 50-50 avec ARM, avec une production en propre de 1,857 t de Pt, 1,608 t de Pd, 0,317 t de Rh et, en 2023, 0,488 t de Ru, 0,115 t de Ir, 0,065 t d’or, 55 000 t de chromite, 428 t de Ni et 262 t de Cu.
Les réserves prouvées et probables sont de 1 448 millions de t renfermant 3,14 g/t de Pt, Pd, Rh et Au.
- Impala Platinum (Implats), a produit, en 2023-24, 49,455 t de platine, 36,018 t de palladium, 5,910 t de rhodium, 16 200 t de nickel et en 2020-21, 8,709 t de ruthénium, 2,115 t d’iridium, 3,931 t d’argent, 2,936 t d’or, 11 900 t de cuivre et 100 t de cobalt. La répartition des revenus du groupe sont, en 2024, par métaux, de 18 % pour le rhodium, 28 % pour le palladium, 32 % pour le platine, 5 % pour le nickel, 17 % pour les autres métaux. Implats exploite 4 complexes miniers en Afrique du Sud, 2 au Zimbabwe et 1 au Canada :
- en Afrique du Sud, les mines d’Impala Rustenburg, détenues à 87 %, qui ont donné, en 2023-24, en métaux raffinés, 20,538 t de Pt, 9,502 t de Pd, 2,411 t de Rh, 3 704 t de Ni,
- celles de Impala Bakofeng, depuis juin 2023, après la prise de contrôle de Royal Bakofeng Platinium et une production de 8,407 t de Pt, 3,571 t de Pd, 911 kg de Rh et 2 187 t de Ni.
- celles de Marula, à 73,3 % avec contenu dans des concentrés 2,703 t de Pt, 2,687 t de Pd, 554 kg de Rh, 255 t de Ni,
- et celles de Two Rivers, à 46 %, en joint venture avec ARM avec contenu dans des concentrés 4,280 t de Pt, 2,610 t de Pd, 700 kg de Rh, 873 t de Ni,
- au Zimbabwe les mines de Zimplats, à 87 % avec contenu dans des mattes 9,263 t de Pt, 7,879 t de Pd, 815 kg de Rh, 6 108 t de Ni,
- et celle de Mimosa, à 50 %, en joint venture avec Sibanye Stillwater avec contenu dans des concentrés 3,757 t de Pt, 2,918 t de Pd, 317 kg de Rh, 3 697 t de Ni.
- En décembre 2019, a acquis le producteur canadien North American Palladium qui exploite le gisement du Lac des Îles dans l’Ontario. En 2023-24, la production a été de 591 kg de Pt, 7,53 t de Pd et, en 2020-21, 1 247 t de Ni.
Les réserves prouvées et probables sont de 490 millions de t renfermant 3,23 g/t de platinoïdes et or.
- Sibanye Stillwater a acquis en Afrique Australe, Aquarius Platinium, en mars 2016, le complexe de Rustenburg en novembre 2016 puis aux États-Unis, Stillwater Mining, en mai 2017 et Lonmin, en juin 2019. Les productions, dans les mines de platine, en Afrique du Sud, au Zimbabwe et aux États-Unis, ont été, en 2024, de 36,912 t de Pt, 27,302 t de Pd, 5,152 t de Rh, 8,259 t de Ru, 1,990 t de Ir, 955 kg de Au, 2,324 millions de t de chromite. Par ailleurs, Sibanye Stillwater est un important producteur d’or (en 2024, avec 22,870 t) avec ses mines d’or sud-africaines. La répartition des revenus, selon les métaux produits, en 2024, est de 59,5 % pour les platinoïdes, 37,1 % pour Au, 6 % pour Cr, 3,8 % pour Zn, 3,6 % pour Ni, 1 % pour Ag.
- En Afrique du Sud détient la mine de Kroondal avec, en 2024, la production de 5,096 t de Pt, 2,671 t de Pd, 914 kg de Rh, 1,519 t de Ru, 344 kg de Ir et 45,3 kg de Au,
- détient 91 % des rejets miniers de Mile, adjacents à la mine de Kroondal, qui ont donné 919 kg de Pt, 365 kg de Pd, 74,8 kg de Rh, 158 kg de Ru et 59,8 kg de Au
- depuis juin 2019 détient 95,25 % de la mine de Marikana après l’acquisition de Lonmin avec, une production de 14,920 t de Pt, 6,654 t de Pd, 2,278 t de Rh, 3,706 t de Ru, 953 kg de Ir et 276 kg de Au,
- ainsi que le complexe minier de Rustenburg regroupant les mines de Bathopele, Khuseleka, Siphumelele et Thembelani avec une production, en 2024, de 11,055 t de Pt, 5,891 t de Pd, 1,726 t de Rh, 2,730 t de Ru, 622 kg de Ir et 314 kg de Au.
- Au Zimbabwe détient 50 % de la mine Mimosa, avec Impala Platinum et une production de 1,912 t de Pt, 1,485 t de Pd, 159 kg de Rh, 146 kg de Ru, 71 kg de Ir et 260 kg de Au.
- Aux États-Unis, exploite les mines de East Boulder et Stillwater. En 2024, les productions ont été de 3,010 t de Pt et 10,236 t de Pd.
Les réserves prouvées et probables sont en Afrique Australe de 262,5 millions de t de minerai renfermant 3,3 g/t de platinoïdes. Aux États-Unis, les réserves sont de 44,5 millions de t de minerai renfermant 13,3 g/t. En Afrique Australe, les proportions entre les divers éléments sont, selon les mines, comprises entre 46 % et 57 % pour Pt, 24 et 36 % pour Pd, 4 et 9 % pour Rh, 4 et 11 % pour Ru, 2 et 3 % pour Ir et 0,7 et 8 % pour Au alors qu’aux États-Unis elles sont de 78 % de Pd et 22 % de Pt.
- Nornickel, est le quatrième producteur mondial de platine, le cinquième de rhodium et le premier producteur mondial de palladium avec, en 2024, une production de 20,746 t de platine, 85,908 t de palladium, 2,022 t, en 2017, de rhodium. Nornickel est d’abord un producteur de nickel raffiné (n°2 mondial) et de cuivre, avec, en 2024, une production de 205 067 t de nickel et 432 528 t de cuivre, les platinoïdes étant coproduits. La répartition des revenus du groupe sont, en 2021, par métaux, de 37,4 % pour le palladium, 21,2 % pour le cuivre, 20,1 % pour le nickel, 6,1 % pour le rhodium, 3,9 % pour le platine et 7,3 % pour les autres métaux. Le groupe exploite des mines en Russie, dans la péninsule de Taimyr (Polar Division) avec 4 mines souterraines (Komsomolsky, Oktyabrsky, Taimyrsky, Zapolyarny) et une mine à ciel ouvert (Medvezky-Ruchey) et dans celle de Kola (Kola MMC) avec les mines de Severny (souterraine et à ciel ouvert) et Kaula-Kotselvaara. En Russie, les réserves prouvées et probables, fin 2023, sont de 1 267 millions de t de minerai renfermant 0,70 % de Ni, 1,26 % de Cu, 0,88 g/t de Pt, 3,26 g/t de Pd, 0,18 g/t de Au.
- Northam Platinum, exploite 4 mines souterraines dans le complexe du Bushveld, celles de Zondereinde et Eland à l’ouest et les deux de Booysendal, à l’est. En 2023-24, les productions ont été de 16,367 t de platine, 8,279 t de palladium, 2,801 t de rhodium, 5,044 t de ruthénium, 1,067 t d’iridium, 324 kg d’or, 2 042 t de nickel, 1 195 t de cuivre et 1 320 965 t de chromite. Les réserves prouvées et probables sont de 258,6 millions de t de minerai renfermant 3,47 g/t de Pt, Pd, Rh et Au.
- ARM (African Rainbow Minerals) exploite, en Afrique du Sud, les mines de Two Rivers, à 54 % avec 46 % pour Impala Platinum, Modikwa, à 41,5 % avec 50 % pour Anglo American et totalement Bokomi.
- En 2023-24, la production totale de Two Rivers a été de 4,281 t de Pt, 2,610 t de Pd, 699 kg de Rh, 1,089 t de Ru, 280 kg de Ir, 105 kg de Au, 874 t de Ni, 510 t de Cu et 147 904 t de chromite avec des réserves prouvées et probables de 65,32 millions de t de minerai renfermant 3,18 g/t de platinoïdes et or dans la couche UG2 et 0,66 millions de t renfermant 2,04 g/t de platinoïdes et or dans la couche Merensky. La production sous forme de concentrés est totalement vendue à Impala Platinium,
- celle de Modikwa, avec une production totale de 3,722 t de Pt, 3,306 t de Pd, 663 kg de Rh, 961 kg de Ru, 225 kg de Ir, 135 kg de Au, 917 t de Ni, 561 t de Cu et 85 575 t de chromite avec des réserves prouvées et probables de 37,09 millions de t renfermant 4,22 g/t de Pt, Pd, Rh et Au. La production sous forme de concentrés est totalement vendue à Anglo American Platinium,
- La mine de Bokomi a commencé à produire en 2023-24 avec 329 kg de Pt, 354 kg de Pd, 66 kg de Rh, 93 kg de Ru, 23 kg de Ir, 12 kg de Au, 83 t de Ni et 63 t de Cu.
- Royal Bafokeng Platinium, a été acquis par Impala Platinium, en 2023, et est devenu Impala Bafokeng.
- Au Canada, Vale et Glencore extraient des platinoïdes de leurs mines de Nickel au côté de Impala Platinium qui exploite une mine de platinoïdes dans l’Ontario (voir plus haut).
Commerce international : en 2023.
Les États-Unis, ont importé 70 t de platine, 64 t de palladium, 11 t de rhodium, 11 t de ruthénium, 1,9 t d’iridium. Ils ont exporté 12 t de platine, 34 t de palladium, 0,18 t de rhodium et 0,62 t des autres platinoïdes.
Recyclage et stocks
L’une des caractéristiques des platinoïdes est leur grande capacité à être recyclés. Lorsqu’ils sont recyclés, plus de 96 % du métal contenu est récupéré.
En 2024, dans le monde :
- 42,6 t de platine ont été recyclées provenant, à 79,1 % de la catalyse automobile, 16,9 % de la bijouterie et 2,7 % d’applications électriques, électroniques et autres. En 2021, 30,9 % provient d’Amérique du Nord, 27,1 % d’Europe de l’Ouest, 18,7 % de Chine, 12,5 % du Japon.
- 91,5 t de palladium ont été recyclées provenant à 83,3 % de la catalyse automobile, 16,4 % d’applications électriques, électroniques et autres. En 2021, 47,2 % provient d’Amérique du Nord, 15,9 % d’Europe de l’Ouest, 11,8 % du Japon, 10,3 % de Chine.
- 9,1 t de rhodium ont été recyclées provenant de la catalyse automobile. En 2021, 53,4 % provient d’Amérique du Nord, 17,8 % d’Europe de l’Ouest, 12,3 % du Japon, 2,7 % de Chine.
En Europe, les principales entreprises de recyclage de platinoïdes sont soit des métallurgistes comme Umicore, à Hoboken, en Belgique ou Heraeus, en Allemagne ou des fabricants de catalyseurs comme BASF, en Allemagne.
Aux États-Unis, le groupe Sibanye Stillwater dans son complexe métallurgiques de Colombus dans le Montana, traite les minerais de ses mines de Stillwater et East Boulder avec une production, en 2024, de 13,246 t de platinoïdes et procède au recyclage de déchets, principalement de pots catalytiques, avec une production de 9,843 t de platinoïdes.
Stock gouvernementaux :
Jusqu’en 2005, les productions russes de platinoïdes n’étaient pas connues, on connaissait seulement le résultat du déstockage des stocks accumulés, ceux-ci étant secret d’État. En 2003, le stock de palladium était estimé à 370 t. Entre 2005 et 2012, les ventes du stock russe ont porté sur 237 t de palladium.
En 1994, le stock des États-Unis était de 13,7 t de platine, 39,3 t de palladium et 920 kg d’iridium. Entre 1999 et 2007 la vente de ce stock a eu lieu et il reste, en 2023, un stock résiduel de 261 kg de platine et 15 kg d’iridium.
Stocks financiers :
Les ETF (Exchange Traded Funds) sont des fonds cotés en bourse qui émettent des actions reposant sur des stocks physiques de métal. Ils ont été créés, en 2007 pour le platine et le palladium et en 2011 pour le rhodium. Fin 2017, ils étaient estimés à 80,1 t de platine, 41,2 t de palladium et 2,7 t de rhodium.
Situation française
En 2024.
Pas de production primaire.
Exportations :
- Platine brut ou en poudre : 1 493 kg à 51 % vers l’Italie, 20 % la Suisse, 20 % le Royaume Uni, 5 % l’Allemagne.
- Palladium brut ou en poudre : 1 747 kg à 34 % vers la Suisse, 32 % l’Italie, 31 % vers l’Espagne.
- Rhodium brut ou en poudre : 10,1 kg à 74 % vers l’Allemagne, 20 % la Suisse, 3 % le Maroc.
- Autres platinoïdes brut ou en poudre : 13,5 kg, à 59 % vers l’Italie.
Importations :
- Platine brut ou en poudre : 476 kg à 31 % de Colombie, 21 % d’Italie, 17 % de Suisse, 12 % des États-Unis, 3 % d’Allemagne.
- Palladium brut ou en poudre : 1 424 kg à 34 % d’Espagne, 31 % d’Italie, 23 % de Suisse, 4 % des États-Unis.
- Rhodium brut ou en poudre : 8,1 kg à 65 % d’Italie, 28 % d’Allemagne, 6 % de Suisse.
- Autres platinoïdes brut ou en poudre : 266,2 kg à 68 % d’Allemagne, 19 % d’Italie, 11 % de Suisse.
Utilisations
Consommations
Répartition, en 2023.
|
Platine |
|
Palladium |
|
Rhodium, en 2015 |
Chine |
29,4 % |
|
21,6 % |
|
20 % |
Europe |
20,9 % |
|
21,8 % |
|
26 % |
Amérique du Nord |
16,3 % |
|
21,0 % |
|
26 % |
Japon |
9,7 % |
|
10,4 % |
|
12 % |
Total mondial, en 2024 |
244,8 t |
|
314,0 t |
|
32,5 t en 2024 |
Source : Johnson Matthey
Consommations mondiales des autres platinoïdes, en 2024 :
Ruthénium : 37,3 t.
Iridium : 7,4 t.
Osmium : moins d’une t/an.
Secteurs d’utilisation
Dans le monde.
La catalyse automobile est, de très loin, le principal secteur d’utilisation des platinoïdes, elle compte pour 56 % des emplois du platine, du palladium et du rhodium réunis.
- Pour les véhicules fonctionnant à l’essence, c’est principalement le palladium, associé au rhodium qui est utilisé. Lorsque le platine est utilisé, il est associé au palladium et au rhodium. Dans les pots catalytiques 3 voies, le platine ou le palladium permettent la conversion du CO et des hydrocarbures imbrûlés en CO2 et en eau alors que le rhodium permet la conversion des oxydes d’azote en diazote et eau lorsque le rapport air/carburant est de 14,7. La teneur en platinoïdes est de 2 à 3 g par véhicule.
- Pour les véhicules diesel, c’est principalement le platine qui est utilisé, avec une teneur en platinoïdes de 7 à 8 g par véhicule.
Platine
En 2024, dans le monde. Source : Johnson Matthey
Catalyse automobile |
46,4 % |
|
Médical |
3,7 % |
Bijouterie |
18,7 % |
|
Contrôle pollution |
3,6 % |
Chimie |
8,6 % |
|
Électronique |
3,3 % |
Verre |
6,1 % |
|
Pétrole |
2,0 % |
Source : Johnson Matthey
L’Europe, avec, en 2023, 31,3 t de platine consommées en catalyse automobile représente 30,5 % de la consommation de ce secteur.
La Chine avec, en 2023, 14,8 t de platine consommées en bijouterie, représente 35,0 % de la consommation de ce secteur.
Le platine est utilisé en catalyse chimique principalement pour fabriquer des silicones mais aussi pour la synthèse du paraxylène destiné à produire de l’acide téréphtalique puis du polyéthylène téréphtalate (PET). Il est également employé dans les toiles permettant de catalyser l’oxydation de l’ammoniac en oxyde d’azote lui même transformé en acide nitrique. En général, le catalyseur est peu consommé lors de son utilisation et au bout d’un certain temps est facilement recyclable, sauf dans le cas de la fabrication des silicones où il est employé dans leur vulcanisation à froid sous forme, en général, d’acide chloroplatinique, H2PtCl4, une partie du catalyseur se trouve incorporé dans le produit final. Par exemple, les silicones des implants mammaires renferment de 6 à 8 µg de Pt/g de silicone, soit plus que la teneur des minerais sud-africains.
Le platine, permet de catalyser la réaction du dihydrogène avec le dioxygène, avec formation d’eau, à la base du fonctionnement des piles à combustible.
Dans l’industrie verrière, le platine, allié à 5 à 20 % de rhodium, est employé dans la confection de filières pour la production de fibre de verre, d’un diamètre compris entre 5 et 13 µm et pour la fabrication d’écrans à cristaux liquide (LCD).
En électronique, le platine est utilisé à 95 % dans la fabrication de disques durs, sous forme d’alliages cobalt–chrome-platine, dans des couches minces magnétiques d’environ 20 nm.
Le platine a de nombreuses autres applications, du fait de sa résistance à la corrosion, en particulier à haute température. Il est employé comme creuset pour diverses fusions, dans des thermocouples (platine/platine-rhodié), comme électrodes, en particulier dans les pacemakers, comme revêtement, sous forme d’alliage avec l’aluminium, de pales de turbines de réacteurs…
Palladium : en 2024.
Catalyse automobile |
84,3 % |
|
Dentaire et médical |
1,8 % |
Chimie |
5,5 % |
|
Contrôle pollution |
1,3 % |
Électronique, électricité |
5,4 % |
|
Bijouterie |
0,8 % |
Source : Johnson Matthey
En électronique, le palladium est utilisé pour la fabrication de condensateurs céramiques multicouches ainsi que pour remplacer l’or dans les dépôts destinés à faciliter les connexions électriques.
En chimie, dans la fabrication de l’acide nitrique, le catalyseur est constitué de plus de 50 toiles de platine rhodié de plus de 4 mètres de diamètre, avec un fil d’environ 0,07 mm de diamètre. Les pertes en platine varient entre 25 et 40 mg/t de HNO3 pur. Elles sont dues à un effet mécanique et à l’oxydation du platine en PtO2. Le platine perdu par effet mécanique est en partie récupéré dans des filtres. Celui qui est oxydé peut être, en partie, récupéré par ajout de toiles de palladium sur lesquelles l’oxyde de platine est réduit selon la réaction :
PtO2 + 2 Pd = Pt + 2 PdO
A une température supérieure à 750°C, l’oxyde de palladium est décomposé en palladium qui forme un alliage métallique avec le platine. Ainsi, plus de 80 % du platine et 30 % du rhodium peuvent être récupérés. La durée moyenne de vie du catalyseur est comprise entre 3 et 18 mois.
Par ailleurs, en chimie, le palladium est utilisé comme catalyseur dans la purification de l’acide téréphtalique et dans la fabrication du peroxyde d’hydrogène.
L’utilisation dentaire du palladium est surtout importante au Japon, ce pays représentant, en 2018, avec 5 t, 44 % des utilisations dans ce secteur, sous forme d’un alliage avec l’or, appelé « kinpala », renfermant 20 % de palladium.
Le palladium déposé sur des zéolithes, adsorbe l’éthylène et est employé pour retarder le mûrissement des fruits et légumes frais lors de leur stockage. Il adsorbe également le dihydrogène et est utilisé pour sa purification à l’aide de membranes en alliage palladium-argent.
Rhodium : en 2024.
Catalyse automobile |
88,9 % |
|
Électronique |
0,6 % |
Chimie |
9,2 % |
|
|
|
Source : Johnson Matthey
Le rhodium est utilisé en catalyse chimique dans la production d’acide acétique, d’oxo-alcools ainsi que comme élément d’alliage des catalyseurs de platine et des filières de platine utilisées dans l’industrie verrière.
Ruthénium : en 2024.
Chimie |
46,6 % |
|
Électrochimie |
11,8 % |
Électronique, électricité |
29,2 % |
|
Autres |
12,3 % |
Source : Johnson Matthey
Le ruthénium est utilisé comme catalyseur dans la production d’ammoniac à partir de gaz naturel et avec l’iridium, comme revêtement d’électrodes dans l’électrolyse de saumures pour la fabrication du dichlore et de l’hydroxyde de sodium. Il est aussi employé, avec le platine, comme catalyseur dans les piles à combustible. L’ajout de 0,1 % de Ru au titane permet d’augmenter considérablement sa résistance à la corrosion. En Chine, il est employé comme catalyseur dans la production de caprolactame et d’acide adipique destinés à la production de nylon 6 et 6.6. Le ruthénium est également utilisé pour élaborer des cibles de pulvérisation cathodique pour des dépôts en couche mince sur les disques durs. Ces dépôts, très minces, de 4 couches atomiques, séparent deux couches magnétiques pour créer un couplage antiferromagnétique qui permet d’augmenter la densité du stockage sur le disque dur.
Iridium : en 2024.
Électrochimie |
44,6 % |
|
Électronique, électricité |
13,5 % |
Chimie |
16,2 % |
|
Autres |
25,7 % |
Source : Johnson Matthey
L’iridium est utilisé avec le ruthénium comme revêtement d’électrodes dans l’électrolyse de saumures pour la fabrication du dichlore et de l’hydroxyde de sodium. Il est également employé pour élaborer des creusets destinés à la fabrication de monocristaux de saphir. Il a été utilisé dans l’alliage (90 % Pt – 10 % Ir) du mètre étalon réalisé par George Matthey et livré au gouvernement français le 4 octobre 1879.
L’osmium, qui s’oxyde à l’air lorsqu’il est à l’état divisé en donnant du tétroxyde (OsO4), très toxique, est employé dans les revêtements d’or sur verre. Le tétroxyde d’osmium est utilisé dans la détection des empreintes digitales et des traces d’ADN lors des enquêtes de la police scientifique.
Bibliographie
- Données issues du site de Johnson Matthey, Orchard Road, Royston, Hertfordshire, SG8 5HE, Royaume Uni.
- PGM market report, Johnson Matthey, mai 2025.
- J.F. Labbé, J.J. Dupuy, « Panorama 2012 du marché des platinoïdes« , Rapport public BRGM/RP-63169-FR, janvier 2014.
- M. Leguérinel « En proie à des difficultés systémiques, l’Afrique du Sud continue malgré tout d’asseoir sa domination sur la production de platinoïdes« , Mineral Info, nov. 2020.
- M. Leguérinel et A. Bouallou, « Fiche de criticité – Iridium« , BRGM, COMES, septembre 2020.
- M. Leguérinel et A. Bouallou, « Fiche de criticité – Ruthénium« , BRGM, COMES, septembre 2020.
- DERA Rohstoffinformationen, Platin, Palladium, Rhodium, 2015.
- Heraeus, « PGM supply-demand balance« .
- Base de données physiques, chimiques, mécaniques sur les métaux du groupe du platine : PGM Database, Johnson Matthey, Anglo American, IPA.
- International Platinum Group Metals Association (IPA), Schiess-Staett-Strasse 30, 80339 Munich, Allemagne.
- World Platinum Investment Council, 64 St James’s Street, SW1A 1NF, Londres, Royaume Uni.
- Jean-François Moyen, Le complexe du Busveld, janvier 2007.
- R.P. Schouwstra, E.D. Kinloch, C.A. Lee, « A short geological review of the Bushveld complex », Platinum Metal Rev., 2000, 44 (1), 33-39.
- D.R. Wilburn, « Global exploration an production capacity for platinum-group-metals from 1995 through 2015« , USGS, décembre 2012.
Archives
Platinoïdes 2023
Platinoïdes 2022
Platinoïdes 2019
Platinoïdes 2014
Platinoïdes 2012
Commentaires récents