Données industrielles
Matières premières
Avec une teneur, en masse, de 5 %, le fer est, après l’aluminium, le 2ème élément métallique le plus répandu dans l’écorce terrestre.
Minerais :
Le fer est présent sous forme oxydée, Fe2O3 (hématite) ou parfois Fe3O4 (magnétite), avec des teneurs en fer comprises entre 30 %, pour les minerais pauvres, et 66 %, pour les minerais riches. La teneur en fer d’un minerai constitué d’hématite pure serait de 69,94 %.
Une partie de la production brésilienne est sous forme d’itabirite qui est un minerai de fer (hématite, magnétite), métamorphisé, en présence de quantités importantes de quartz, avec des teneurs en fer comprises entre 37 et 52 %.
Principaux complexes miniers : en 2024 (2023-24 pour BHP Billiton et FMG).
en millions de t de minerai
Complexe minier |
Exploitant |
Production |
|
Complexe minier |
Exploitant |
Production |
Hamersley, Australie |
Rio Tinto |
225 |
|
Solomon Hub, Australie |
FMG |
75 |
Area C, Australie |
BHP Billiton |
106 |
|
Jimblebar, Australie |
BHP Billiton |
73 |
Chichester Hub, Australie |
FMG |
100 |
|
Newman, Australie |
BHP Billiton |
58 |
Carajás-Serra Norte, Brésil |
Vale |
88 |
|
Vargem Grande, Brésil |
Vale |
37 |
Serra Sul, Brésil |
Vale |
83 |
|
Yandi, Australie |
BHP Billiton |
18 |
Sources : rapports des sociétés
Environ 98 % de la production minière de fer est destinée à l’élaboration de l’acier.
Ferrailles :
Leur part dans la production d’acier est importante. Voir plus loin.
Production minière de fer
En 2024, en millions de t de fer contenu sur un total mondial de 1 600 millions de t. Source : USGS
Production minière de fer : en 2024, en fer contenu, sur un total mondial de 1 600 millions de t.
en millions de t de fer contenu
Australie |
580 |
|
Afrique du Sud |
42 |
Brésil |
280 |
|
Canada |
32 |
Chine |
170 |
|
États-Unis |
30 |
Inde |
170 |
|
Ukraine |
26 |
Iran |
59 |
|
Suède |
20 |
Russie |
53 |
|
Pérou |
14 |
Source : USGS
Les teneurs des minerais varient en moyenne de 30 % pour la Chine à 66 % pour le Brésil.
Les principaux gisements australiens, à ciel ouvert, sont situés dans la région de Pilbara au nord-ouest de l’Australie occidentale. Ils sont exploités, en particulier, par Rio Tinto, BHP-Billiton et FMG.
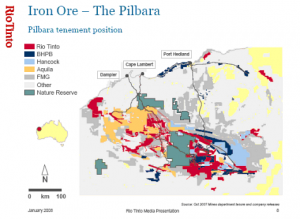
En Russie, les principales mines exploitent l’Anomalie Magnétique de Koursk (KMA), située en Russie centrale. Le gisement actuellement exploité, à ciel ouvert, à 220-270 m de profondeur, est constitué de quartzites ferrugineuses contenant de 34 à 39 % de fer. Ce gisement constitue la deuxième plus grande ressource de fer, dans le monde.
En 2025, devrait commencer l’exploitation à ciel ouvert du gisement guinéen de Simandou. Le gisement est concédé d’une part à Simfer, coentreprise entre Rio Tinto avec 53 % et Chalco Iron Ore Holdings (CIOH) avec 47 %, détenant 85 % d’une partie du gisement, les 15 % restant étant détenus par l’État guinéen et d’autre part à Winning Consortium Simandou (WCS), groupe de Singapour associé à des intérêts chinois et à l’État guinéen.
Le gisement de Simandou, situé au sud-est de la Guinée s’étend sur 8 km de long et 1 km de large. La partie concédée à Simfer possède des réserves prouvées et probables de 1,5 milliard de t contenant 65,3 % de fer. La production prévue à compter de 2027 est de 60 millions de t/an de minerai et la durée d’exploitation de 26 ans. Le minerai est évacué par une ligne de chemin de fer, le Transguinéen détenu à 42,5 % par Simfer, 42,5 % par WCS et 15 % l’État guinéen, de 650 km jusqu’au port en eau profonde de Morebaya au sud de Conakry.
Principaux producteurs :
Sources : rapports des sociétés
- Au Brésil, Vale, exploite du minerai de fer, à ciel ouvert, dans principalement 3 ensembles (Nord, dans l’État de Pará, Sud-Est et Sud dans l’État de Minas Gerais) et partage moitié-moitié, avec BHP-Billiton, les mines de Samarco dans l’État de Minas Gerais.
Les réserves prouvées et probables de Vale sont, fin 2024, de 12,1 milliards de t contenant, en moyenne, 54,2 % de fer.
- La production de l’ensemble Nord, à Carajás, avec 3 mines, a été, en 2024, de 177,5 millions de t de minerai contenant 66,7 % de fer sous forme d’hématite. Les mines de Carajás ont été découvertes en 1967 et leur production a débuté en 1986. Les réserves prouvées et probables sont de 5,3 milliards de tonnes de minerai contenant 65,2 % de fer. La mine produit également du minerai de cuivre, de manganèse, d’or. Le minerai, qui ne nécessite pas d’enrichissement, est acheminé, en 30 heures, par voie ferrée (16 convois/jour de 330 wagons), sur 892 km, jusqu’au port de São-Luis. La construction de la voie ferrée a compté pour 56 % des investissements, l’infrastructure minière pour 20 %, l’ensemble portuaire pour 14 %. Au total, de la mine au port, 4 000 personnes sont employées.
- L’ensemble Sud-Est, sur 3 sites et 8 mines, a produit, en 2024, 86,9 millions de t avec des réserves de 2,7 milliards de t contenant, en moyenne, 48,7 % de fer. Le minerai d’itabirite, contient de 35 à 60 % de fer, il doit être concentré.
- L’ensemble Sud, sur 3 sites et 9 mines, a produit, en 2024, 63,3 millions de t avec des réserves de 4,0 milliards de t contenant, en moyenne, 43,5 % de fer.
- Les mines de Samarco, ont arrêté jusqu’en décembre 2020 toute production après la rupture d’une digue de retenue d’un bassin de rétention de résidus miniers, le 5 novembre 2015, qui a entraîné la mort de 19 personnes dans le village de Mariana. En 2024, la production des mines de Samarco a été de 9,6 millions de t.
En 2023, la production de Vale a été destinée à 77 % à l’Asie dont 62 % à la Chine, 12 % au Brésil, 5 % à l’Europe.
- En 2024, la production de Rio Tinto a été réalisée à 96,7 % en Australie et 3,3 % au Canada. Le total des réserves prouvées et probables de Rio Tinto représente 3,140 milliards de t de minerai renfermant 62,7 % de fer.
- La production australienne a été réalisée sur le gisement de Pilbara, avec 16 mines en activité, 4 ports d’exportation du minerai et 1 700 km de voies ferrées. Cette exploitation est effectuée à travers plusieurs sociétés : Hamersley Iron possédée en propre, Channar et Eastern Range en joint venture avec des sociétés chinoises, Hope Down en association 50-50 avec Hancock Prospecting, Robe River Iron Associates détenue à 53 % par Rio Tinto, associé à des sociétés japonaises (Mitsui, Nippon Steel et Sumitomo). Les réserves australiennes prouvées et probables de Rio Tinto sont de 2,23 milliards de t de minerai renfermant 60,9 % de fer. Début 2022 a commencé la production de la mine de Gudai-Darri avec 50 millions de t/an pouvant être portée à 70 millions de t/an avec des réserves prouvées et probables de 561 millions de t renfermant 61,8 % de fer.
- Par ailleurs, Rio Tinto détient 58,7 % de la société Iron Ore Company of Canada qui exploite à ciel ouvert un gisement au Canada, à Labrador City. L’exploitation minière canadienne possède 235 millions de t de réserves prouvées et probables contenant 65,0 % de fer. En 2024, la production en propre a été de 9,446 millions de t acheminées par 418 km de voies ferrées jusqu’au port de Sept-îles, au Québec.
- La production de BHP-Billiton, en Australie, a été, en 2023-24, réalisée totalement sur le gisement de Pilbara, par la société Western Australia Iron Ore (WAIO) avec 4 joint ventures détenues à 85 % (Mt Newman, Area C, Yandi et Jimblebar) avec les groupes japonais Mitsui et Itochu, le minerai étant acheminé par 1 000 km de voies ferrées vers 2 ports situés à Port Hedland. L’exploitation la plus importante, Mt Whaleback, détenue par la joint venture Mt Newman, a débuté en 1968 et s’étend sur une surface de 5×1,5 km, avec un minerai titrant 68 % de fer. C’est la plus importante mine de fer au monde, à ciel ouvert, d’un seul tenant.
Les réserves prouvées et probables de BHP-Billiton sont, en Australie, de 4,32 milliards de t à 62,0 % de Fe.
- Par ailleurs, BHP-Billiton détient moitié-moitié avec Vale, la société Samarco qui exploite des gisements au Brésil, avec, en 2014-15, une production revenant à BHP-Billiton de 14,5 millions de t. Les mines de Samarco, ont arrêté jusqu’en décembre 2020 toute production après la rupture d’une digue de retenue d’un bassin de rétention de résidus miniers, le 5 novembre 2015, qui a entraîné la mort de 19 personnes dans le village de Mariana. En 2023-24, la production revenant à BHP est de 4,748 million de t.
- Fortescue Metals Group (FMG), exploite 3 complexes miniers dans la région de Pilbara au nord-ouest de l’Australie occidentale, Chichester avec les mines de Cloudbreak et Christmas Creek et Solomon avec les mines de King Valley et Firetail. Le minerai est acheminé par 620 km de voies ferrées jusqu’au port de Herb Helliot. Les réserves sont de 1,701 milliard de t de minerai d’hématite renfermant 57,4 % de Fe et de 832 millions de t de minerai de magnétite renfermant 67,3 % de Fe. En 2023 a débuté l’exploitation de magnétite sur le complexe minier de Iron Bridge.
- Anglo American exploite à ciel ouvert des mines de fer :
- En Afrique du Sud avec 52,5 % de la société Kumba Iron Ore qui a produit, en 2024, 35,7 millions de t de minerai en exploitant les mines de Kolomela avec des réserves prouvées et probables de 116 millions de t renfermant 63,0 % de fer et Sishen avec des réserves prouvées et probables de 425 millions de t renfermant 64,0 % de fer.
- Au Brésil avec le complexe de Minas-Rio qui exploite la mine de Serra do Sapo, avec, en 2024, une production de 25,0 millions de t et des réserves prouvées et probables de 1,648 milliard de t renfermant 67,0 % de fer.
- ArcelorMittal exploite des mines de fer dans divers pays qui fournissent près de la moitié des besoins du groupe :
- Au Canada, avec la mine à ciel ouvert de Mont Wright, au Nord-Ouest du Québec, exploitées à 85 % par la filiale AMEN. Le minerai est acheminé, par la filale AMIC, par une voie ferrée privée de 420 km jusqu’à Port Cartier sur de Saint-Laurent. En 2024, la production a été de 24,2 millions de t, dont 20,5 millions de t pour Arcelor et les réserves prouvées et probables sont de 1,735 milliard de t renfermant 29,1 % de fer. En 2017, a débuté l’exploitation commerciale, par la société Baffinland avec une participation de 25,23 % d’ArcelorMittal, du gisement de Mary River, en Terre de Baffin, province du Nunavut. En 2024, la production est de 5,8 millions de t, dont 1,5 million de t pour Arcelor et la capacité de production doit être augmentée pour atteindre 12 millions de t/an. Les réserves sont de 165 millions de t renfermant 64,1 % de fer.
- En Ukraine, avec la mine de Kryviy exploitée à ciel ouvert qui a produit, en 2024, 8,0 millions de t, dont 7,6 millions de t pour Arcelor avec des réserves prouvées et probables de 478 millions de t renfermant 33,6 % de fer et souterrainement avec une production de 0,2 million de t et des réserves prouvées et probables de 14 millions de t renfermant 54,3 % de fer.
- Au Brésil, avec 2 mines à ciel ouvert qui ont produit, en 2024, 2,9 millions de t avec des réserves prouvées et probables de 424 millions de t renfermant 40,9 % de fer.
- Au Mexique, avec la mine à ciel ouvert de Las Truchas qui a produit, en 2024, 1,0 million de t et la mine Volcan, à ciel ouvert, qui a produit 0,2 million de t avec des réserves prouvées et probables de 84 millions de t renfermant 28,2 % de fer et 50 % de la mine à ciel ouvert de Peña Colorada qui a produit 2,7 millions de t, dont 1,4 pour Arcelor avec des réserves prouvées et probables de 122 millions de t renfermant 19,7 % de fer.
- Au Kazakhstan, 3 mines à ciel ouvert ont produit, en 2023, 1,4 million de t et possèdent des réserves prouvées et probables de 109 millions de t renfermant 40,5 % de fer et une mine souterraine a produit 1,0 million de t avec des réserves prouvées et probables de 6 millions de t renfermant 41,6 % de fer. Ces mines ont été vendues en décembre 2023.
- Au Liberia, avec la mine à ciel ouvert de Yekepa détenue à 85 %, qui a produit, en 2024, 3,8 millions de t, dont 3,2 millions de t pour Arcelor avec des réserves prouvées et probables de 727 millions de t renfermant 42,9 % de fer. Le minerai est acheminé à l’aide d’une voie ferrée de 260 km jusqu’au port de Buchanan.
- En Bosnie, avec la mine d’Omarska, à ciel ouvert, détenue à 51 %, qui a produit, en 2024, 1,0 million de t, dont 0,5 million de t pour Arcelor avec des réserves prouvées et probables de 3 millions de t renfermant 46,1 % de fer.
- Par ailleurs, détient, en Inde, une participation de 60 % qui a produit 9,8 millions de t, dont 5,9 millions de t pour Arcelor avec des réserves prouvées et probables de 79 millions de t renfermant 57,6 % de fer.
- Metalloinvest est le principal producteur russe avec, en 2021, 57 % de la production russe. Exploite deux mines, Lebedinsky et Mikhailovsky sur l’Anomalie Magnétique de Koursk (KMA), située en Russie centrale. Les réserves prouvées et probables sont de 15,4 milliards de t de minerai.
Commerce international : en 2024.
Principaux pays exportateurs sur un total mondial de 1 691 millions de t de minerais et concentrés.
en millions de t de minerai
Australie |
911 |
|
Ukraine |
34 |
Brésil |
389 |
|
Chine |
25 |
Afrique du Sud |
62 |
|
Pérou |
23 |
Canada |
61 |
|
Malaisie |
22 |
Inde |
36 |
|
Chili |
15 |
Source : International Trade Center
En 2017, les gisements de l’Australie de l’Ouest représentent 94 % des exportations australiennes et 57 % du commerce maritime mondial de minerai de fer. Ces exportations sont destinées, en 2024, à 85 % à la Chine, 6 % au Japon, 5 % à la Corée du Sud. Par ailleurs les gisements de la région de Pilbara représentent 61 % des importations de la Chine. Les exportations depuis Port Hedland ont été de 472 millions de t, celles depuis Cape Lambert de 177 millions de t, celles depuis Dampier de 127 millions de t.
Le Brésil exporte 87 % de sa production et ses exportations représentent, en 2017, 24 % du commerce maritime mondial de minerai de fer.
Principaux pays importateurs sur un total mondial de 1 639 millions de t de minerais et concentrés.
en millions de t de minerai
Chine |
1 237 |
|
Taipei chinois |
20 |
Japon |
96 |
|
Vietnam |
18 |
Corée du Sud |
69 |
|
Indonésie |
14 |
Allemagne |
35 |
|
Bahreïn |
14 |
Malaisie |
21 |
|
Oman |
12 |
Source : International Trade Center
Les importations chinoises proviennent à 60 % d’Australie, 20 % du Brésil, 3 % d’Afrique du Sud.
Réserves minières de minerai de fer
En 2024, en milliards de t de fer contenu sur un total mondial de 88 milliards de t. Source : USGS
en milliards de t de fer contenu sur un total de 88 milliards de t
Australie |
27 |
|
Canada |
2,3 |
Brésil |
15 |
|
Ukraine |
2,3 |
Russie |
14 |
|
États-Unis |
2,3 |
Chine |
6,9 |
|
Iran |
1,5 |
Inde |
3,4 |
|
Pérou |
1,5 |
Source : USGS
En 2021, le groupe russe Metalloinvest possède des réserves de minerai de 15,4 milliards de t devant le groupe Vale (Brésil) avec13,8 milliards de t et BHP Billiton (Australie) avec 4,45 milliards de t.
Situation française : en 2024.
Le minerai exploité jusqu’en 1997 était pauvre et phosphoreux (la minette de Lorraine). Il contient de 30 à 34 % de fer et 0,7 % de phosphore. La production, située en Lorraine, était effectuée souterrainement, par exemple, en 1980, à l’aide de 23 puits. Depuis août 1993, la sidérurgie française s’approvisionne exclusivement en minerai importé, le minerai produit ensuite, de 1993 à 1997, étant exporté au Luxembourg.
Évolution de la production française : le maximum a été atteint en 1960 avec 67 millions de t de minerai (c’était la 3ème production mondiale après celles de l’URSS et des États-Unis), en 1974 la production était de 54 millions de t et, en 1991, de 7,5 millions de t. En plus de 200 ans, 3 milliards de t de minette ont été extraites.
Après la fin de l’extraction lorraine, deux petites exploitations minières ont fonctionné pour alimenter des clients tels que les cimenteries. La mine de Batère (66) avec 3 à 4 personnes et 6 000 t/an qui a fermé en 2001 et celle de Rougé (44) avec une douzaine de personnes qui extrayait quelques dizaines de milliers de t/an a fermé en 2003.
Les réserves sont estimées à 800 millions de t de fer contenu.
Commerce extérieur :
Les exportations étaient de 95 222 t de minerai avec comme principaux marchés à :
- 88 % l’Allemagne,
- 4 % l’Espagne,
- 2 % la Suisse.
Les importations s’élevaient à 9 865 589 t de minerai en provenance principalement à :
- 52 % du Canada,
- 22 % du Brésil,
- 12 % du Liberia,
- 9 % des États-Unis.
Sidérurgie
L’acier, après le bois et le béton est le matériau le plus utilisé dans le monde devant les matières plastiques.
L’acier est constitué principalement de fer, avec des teneurs en carbone inférieures à 1 % (formellement inférieures à 2 %, des teneurs supérieures donnent la fonte) et contient des ajouts, en quantités variables, de divers éléments. Sa composition, mais aussi les traitements thermiques subis, son revêtement de surface… font de l’acier un matériau comprenant de très nombreuses nuances (plus de 3 500) chacune adaptée à un emploi particulier. De plus, c’est un matériau en perpétuelle évolution.
Remarque : les aciers inoxydables, l’acier zingué, le fer chromé et le fer blanc, sont traités dans des chapitres particuliers.
Fabrication de l’acier à partir de minerai
La fabrication de l’acier est réalisée soit à partir de minerai pour 72 % de la production mondiale soit à partir de ferrailles pour 28 % de la production mondiale, voir la partie recyclage.
Principe
La réduction de l’oxyde de fer contenu dans le minerai est réalisée par le monoxyde de carbone formé à partir de coke dans un haut fourneau qui donne de la fonte. La température de fonctionnement du haut-fourneau permet d’obtenir de la fonte liquide surmontée d’un laitier également liquide renfermant une grande partie des impuretés. L’élaboration de la fonte est suivie par son affinage, par oxydation partielle du carbone, dans un convertisseur qui donne de l’acier, puis par un laminage à chaud et/ou à froid qui donne des produits longs (rails…) ou plats (tôles…).
Évolutions
Hauts fourneaux : développement de l’injection de charbon aux tuyères (de 130 à 200 kg/t de fonte) et de l’automatisation du fonctionnement (5 800 capteurs pour le haut fourneau n°4 de Dunkerque). L’injection de charbon permet de réduire la consommation de coke qui est ainsi d’environ 300 kg/t de fonte.
La durée de vie d’un haut fourneau est de l’ordre de 25 ans, la durée de fonctionnement en continu, entre deux réparations, de 12 ans, en moyenne.
Convertisseurs : un ajout de ferrailles peut être effectué à ce niveau.
- par lance : LD (Linz-Donawitz), OLP (Oxygène-Lance-Poudre), LD-AC (LD-Arbed-CRM).
- par le fond : LWS (Loire-Wendel-Sidelor).
- par soufflage mixte (fond et lance) : par exemple, LBE (Lance-Brassage-Equilibre) : insufflation de gaz neutre par le fond d’un convertisseur à lance verticale.
Le développement de ces procédés a été lié à celui de la production massive de O2 transporté par oxyducs (voir le chapitre consacré au dioxygène).
En France, il n’y a plus de convertisseurs Bessemer-Thomas depuis 1980 et de fours Siemens-Martin depuis 1982. En France, fonctionnent 2 aciéries de conversion avec 2 LD à Dunkerque et Fos-sur-Mer.
Métallurgie en poche effectuée entre le convertisseur et la coulée. Elle permet les ajouts nécessaires à la qualité requise de l’acier, son homogénéisation, la désoxydation ou le dégazage (par le vide), la mise en température.
La coulée continue : actuellement concerne près de 97 % de l’acier produit en France. Elle remplace 3 opérations par une seule : coulée en lingots, réchauffage, laminage en demi-produit. L’acier est coulé dans un moule sans fond et donne directement un demi-produit.
Exemple d’une usine intégrée : Fos sur Mer : 4,5 millions de t/an
Réception des matières premières :
- Minerai et charbon : 640 m de quai pour des bateaux de 230 000 t.
- Chaux : le calcaire est extrait d’une carrière située à 25 km : 1 million de t/an, pour alimenter l’usine à chaux.
Préparation des minerais, cokéfaction et agglomération :
- Concassage du minerai : 2 lignes de 300 t/h chacune comportant 3 concasseurs en série.
- Cokerie : traite 2,3 millions de t/an de charbon pour produire 1,73 million de t/an de coke (1,48 pour les hauts-fourneaux, 0,25 pour l’agglomération du minerai), dans 108 fours. La cuisson dure 17,5 h, le coke est éteint par arrosage à l’eau.
- L’agglomération du minerai est réalisée sur une chaîne de 5×110 m. La couche de minerai atteint au maximum 50 cm.
Hauts fourneaux : 2 de 2,5 millions de t/an chacun, soit 7 000 t/jour. Pour chaque haut-fourneau :
- Caractéristiques : volume total : 3 049 m3, diamètre du ventre : 12,89 m, diamètre du creuset : 11,8 m, hauteur totale : 31,43 m, 28 tuyères. Le refroidissement des parois est assuré par de l’eau circulant en circuit fermé entre des plaques. Les hauts fourneaux ont été rénovés en 2007 et 2011.
- Consommations (en kg/t de fonte) : minerai aggloméré : 1 500, minerai calibré : 200, coke : 315, charbon d’injection : 170.
- Chauffage du vent : 3 cowpers avec pour chacun 58 000 m2 de surface de chauffe. Ils permettent d’atteindre des températures de 1250-1300°C.
- Coulée : dans des poches-tonneaux de 450 t dans lesquelles un premier traitement de désulfuration par du carbure de calcium ou de la chaux est pratiqué.
Aciérie : 2 convertisseurs de 335 t.
- Soufflage de dioxygène par lance et par le fond et soufflage de gaz neutres par le fond pour diminuer la teneur en carbone, manganèse et phosphore et éliminer le silicium de la fonte enfournée. Cette opération permet également d’assurer un brassage du liquide et la remontée des impuretés vers le laitier. Addition de chaux pour neutraliser le laitier et de dolomie pour protéger le revêtement réfractaire du convertisseur. Enfournement de ferrailles pour assurer l’équilibre thermique du bain.
- Métallurgie en poche : passage du métal dans des installations de désulfuration puis d’affinage et de mise en température. Lors de la coulée en poches la composition est ajustée par ajout de ferro-alliages.
Coulée continue : 2 installations. Caractéristiques de l’installation la plus récente :
- Capacité de production : 2,43 millions de t/an, vitesse de coulée : 1,8 m/min, largeur : 1,05 à 2,2 m, épaisseur : 0,22 m.
Laminage : par un train à bande de 4,5 millions de t/an de capacité. Caractéristiques :
- 1 cage verticale, 5 cages horizontales dégrossisseuses et 7 cages finisseuses.
- Épaisseurs visées : 1,2 à 20 mm, vitesse maximale de laminage atteinte : 97 km/h.
Bilan énergétique : pour produire 1 t de bobines laminées à chaud.
en millions de joules
Hauts fourneaux |
12 828 |
|
Cokerie |
2 109 |
Laminage à chaud |
3 106 |
|
Coulée continue |
232 |
Agglomération |
2 876 |
|
Convertisseurs |
176 |
Minerais pré-réduits
Dénommés DRI : Direct Reduced Iron ou HBI : Hot Briquetted Iron.
Élaboration :
Les fours électriques d’élaboration de l’acier utilisent principalement de la ferraille. Toutefois, pour des pays producteurs de gaz naturel, il peut être intéressant de réduire du minerai, à l’aide de gaz de synthèse obtenu à partir de gaz naturel ayant subi un reformage, et d’utiliser ce minerai pré-réduit pour alimenter des fours électriques. Le gaz de synthèse peut aussi être produit à l’aide de charbon, c’est le cas pour les 2/3 de la production indienne. Le procédé Midrex, utilisé pour environ 80 % de la production de minerais pré-réduits consiste à traiter, dans un four à cuve, à une température inférieure à 1100°C, le minerai par du gaz naturel reformé qui donne du monoxyde de carbone et du dihydrogène (voir le chapitre dihydrogène). Les réactions mises en jeu sont les suivantes :
Fe2O3 + 3 H2 = 2 Fe + 3 H2O
Fe2O3 + 3 CO = 2 Fe + 3 CO2
La température atteinte ne permet pas la fusion du fer, on obtient une « éponge » de fer. La teneur en fer atteint 92 à 93 % avec 1,4 à 2 % de carbone. Les capacités de production, par installation, peuvent atteindre 1 million de t/an.
D’autres procédés sont employés : four rotatif à l’aide de charbon, HyL, le plus ancien (1957), Fior, en lit fluidisé…
Production : la production mondiale est, en 2024, de 144,1 millions de t dont 0,1 million de t dans l’Union européenne (Allemagne).
en millions de t
Inde |
54,8 |
|
États-Unis |
5,5 |
Iran |
34,1 |
|
Mexique |
4,7 |
Russie |
8,0 |
|
Algérie |
4,2 |
Égypte |
7,1 |
|
Émirats Arabes Unis |
3,5 |
Arabie Saoudite |
6,9 |
|
Qatar |
2,0 |
Source : World steel in figures
Recyclage à partir de ferrailles
Les ferrailles sont principalement utilisées dans des fours électriques à arc. Elles peuvent également être ajoutées, jusqu’à 30 %, à la fonte liquide dans les convertisseurs à oxygène (voir plus haut). Depuis les origines de la fabrication de l’acier, le recyclage a porté, dans le monde, sur 25 milliards de t.
Les ferrailles sont récupérées, broyées (par des broyeurs à marteaux) puis triées magnétiquement.
Le broyeur le plus puissant exploité par la société SIMS Metal Management (Australie, n°1 mondial du recyclage des métaux avec, en 2018, le recyclage de 7,7 millions de t de ferrailles) fonctionnant à Newport (Royaume-Uni) traite à l’heure, 450 véhicules pour donner 350 t de métal.
Origine des ferrailles
Elles proviennent des véhicules hors d’usage, des biens de consommation en fin de vie (électroménager, emballages…), de la démolition de bâtiments… mais aussi, pour 1/3, des chutes neuves de fabrication. Au total, la sidérurgie mondiale recycle, en moyenne, 600 millions de t/an d’acier. En 2017, les taux de recyclage sont de 85 % pour l’acier utilisé dans les constructions, avec une durée de vie de 40 à 70 ans, 90 % pour l’acier utilisé dans les automobiles avec une durée de vie de 7 à 15 ans, 90 % pour l’acier utilisé dans la construction de machines, avec une durée de vie de 10 à 20 ans, 50 % pour l’acier utilisé dans les équipements électriques et les appareil ménagers, avec une durée de vie de 4 à 10 ans. En moyenne, en 2013, le taux de recyclage est de 83 %.
On estime que dans le monde, sont utilisés 200 milliards d’emballages en acier, recyclés à 68 %, soit 7,2 millions de t/an d’acier.
- En France, les taux de recyclage de l’acier sont de 95 % pour les automobiles, 75 % dans le bâtiment et l’électroménager, 62 % pour les emballages.
- Pour chaque tonne d’acier recyclé sont économisés 1,1 t de minerai de fer, 630 kg de charbon, 55 kg de calcaire, 642 kWh et 287 litres de pétrole.
Récupération des ferrailles
En France, en 2014, en millions de t.
- Collecte nationale de ferrailles : 12,9, dont chutes neuves : 2,3, démolition : 1,4, véhicules hors d’usage : 1,2.
- Les ferrailles proviennent à 33,1 % des chutes de la sidérurgie et des industries de transformation de l’acier et 66,9 % de la récupération d’acier usagé.
- Producteurs : n° 1 : Derichebourg qui a traité, en 2017, 3,7 millions de t de ferrailles avec 29 broyeurs-déchiqueteurs.
Commerce international : en 2024.
Principaux pays exportateurs sur un total de 95,8 millions de t, dont 42,6 millions de t par l’Union européenne.
en millions de t
États-Unis |
14,9 |
|
Pays Bas |
6,1 |
Royaume Uni |
7,6 |
|
Canada |
4,9 |
Allemagne |
7,0 |
|
Belgique |
3,5 |
Japon |
6,5 |
|
Pologne |
2,9 |
France |
6,2 |
|
République tchèque |
2,7 |
Source : World steel in figures et ITC
Les exportations des États-Unis sont destinées à 25 % à la Turquie, 20 % au Mexique, 10 % à l’Inde.
Principaux pays importateurs sur un total de 96,7 millions de t, dont 31,7 millions de t dans l’Union européenne.
en millions de t
Turquie |
21,6 |
|
Allemagne |
4,3 |
Italie |
5,9 |
|
Belgique |
4,2 |
États-Unis |
4,7 |
|
Égypte |
3,5 |
Bangladesh |
4,6 |
|
Pays Bas |
3,4 |
Vietnam |
4,6 |
|
Espagne |
3,2 |
Source : World steel in figures et ITC
Les importations turques proviennent à 23 % des États-Unis, 14 % des Pays Bas, 11 % du Royaume Uni, 7 % de Belgique.
Consommations de ferrailles, en 2023. Monde, en 2022 : 630 millions de t, Union européenne, en 2023 : 74,8 millions de t.
en millions de t
Chine |
213,7 |
|
Corée du Sud |
26,1 |
États-Unis |
56,8 |
|
Italie, en 2017 |
21,6 |
Japon |
31,8 |
|
Allemagne, en 2017 |
19,0 |
Turquie |
29,1 |
|
Espagne, en 2017 |
11,1 |
Russie, en 2022 |
29,4 |
|
France, en 2017 |
7,2 |
Source : BIR
Fours électriques à arc
Ils utilisent directement de la ferraille ou des minerais pré-réduits, ces derniers représentant 15 % de la production mondiale d’aciers au four électrique.
Les fours à arc comportent 1 ou 3 électrodes. Les capacités vont de 10 à 220 t. Chaque coulée est effectuée, en moyenne, toutes les 50 à 60 minutes. Les fours les plus performants permettent 30 coulées/jour, le record étant de 7 850 coulées/an. La puissance des fours atteint 0,9 MVA/t, avec une consommation électrique de 320 kWh/t. La consommation de dioxygène est de 30 m3/t.
Les fours électriques à arc à courant continu, plus économiques que ceux à courant alternatif, sont de plus en plus employés.
Consommations, coproduits et émissions de la sidérurgie
Consommations moyennes selon la voie utilisée : en 2018, pour une tonne d’acier brut.
|
Voie haut fourneau – convertisseur |
|
Voie four électrique |
Minerai de fer |
1 370 kg |
|
586 kg |
Charbon |
780 kg |
|
150 kg |
Calcaire |
270 kg |
|
88 kg |
Acier recyclé |
125 kg |
|
710 kg |
Énergie |
19,8 à 31,2 GJ |
|
9,1 à 12,5 GJ |
Source : World Steel Association
- Énergie : la consommation moyenne est, en 2013, de 20,0 GJ/t d’acier brut. En France, en 2013, la consommation d’énergie est de 5,245 millions tep, à partir de charbon et coke métallurgique à 65,2 %, d’électricité à 15,0 %, de gaz naturel à 9,9 %, de charbon et coke énergétique à 9,8 %, de fioul à 0,1 %.
- Eau : 2,5 m3/t d’acier à Sollac Dunkerque.
- Produits réfractaires : 13 kg/t d’acier brut.
Principaux coproduits de la sidérurgie :
- Les laitiers de hauts fourneaux (300 kg/t d’acier) et les scories d’aciéries sont utilisés dans la construction routière, les cimenteries, la fabrication de laine de roche, la fertilisation. Ce sont des coproduits à forte valeur ajoutée. En 2020, la production de l’Union européenne est de 36,3 millions de t et la consommation de 33,2 millions de t à 63 % provenant des hauts-fourneaux et 37 % des aciéries.
Les laitiers des hauts fourneaux sont destinés à 85 % à l’industrie cimentière, 12 % à la construction de routes. Ceux provenant des aciéries sont destinés à 57 % à la construction de routes, 25 % à la métallurgie, 5 % à l’industrie des engrais, 4 % aux cimenteries.
- Les sous-produits des cokeries (sulfate d’ammonium…) sont utilisés en chimie.
Émissions : par t d’acier, dans des installations modernes : 2 kg de poussières, 2,45 kg de SO2. Les émissions de CO2 sont, en 2017, de 1,83 t/t d’acier, elles représentent 7 à 9 % du total des émissions mondiales par les énergies fossiles.
Par ailleurs, les hauts fourneaux sont susceptibles de détruire, par incinération, des déchets de matières plastiques non recyclables. Par exemple, en Allemagne, ces déchets sont introduits, en remplacement de pétrole, dans des hauts-fourneaux.
Productions d’acier brut
Production d’acier brut
En 2024, en millions de t sur un total de 1 883 millions de t. Source Worldsteel
En 2024. Monde : 1 883 millions de t, Union européenne : 129,5 millions de t.
en millions de t
Chine |
1 005,1 |
|
Iran |
31,0 |
Inde |
149,6 |
|
Vietnam |
22,1 |
Japon |
84,0 |
|
Italie |
20,0 |
États-Unis |
79,5 |
|
Taipei chinois |
19,1 |
Russie |
70,7 |
|
Indonésie |
17,0 |
Corée du Sud |
63,5 |
|
Mexique |
13,7 |
Allemagne |
37,2 |
|
Canada |
12,2 |
Turquie |
36,9 |
|
Espagne |
11,8 |
Brésil |
33,7 |
|
France |
10,8 |
Source : Worldsteel
Évolution de la production mondiale d’acier : source : Worldsteel Association
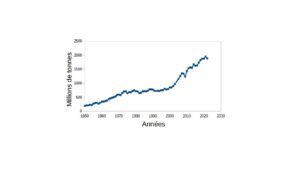
Commerce international
Principaux pays exportateurs : en 2024, sur un total de 449 millions de t, dont 27,8 millions de t pour l’Union européenne.
en millions de t
Chine |
117,1 |
|
Belgique |
15,4 |
Japon |
31,2 |
|
Italie |
15,0 |
Corée du Sud |
28,0 |
|
Vietnam |
13,4 |
Allemagne |
22,6 |
|
Russie |
12,3 |
Turquie |
17,0 |
|
Indonésie |
11,4 |
Source : Worldsteel in figures
Principaux pays importateurs : en 2024, sur un total de 449 millions de t, dont 42,8 millions de t pour l’Union européenne.
en millions de t
États-Unis |
27,3 |
|
Vietnam |
17,2 |
Turquie |
19,7 |
|
Corée du Sud |
14,2 |
Italie |
18,5 |
|
Thaïlande |
13,5 |
Allemagne |
18,3 |
|
Indonésie |
12,8 |
Mexique |
17,6 |
|
Belgique |
11,9 |
Source : Worldsteel in figures
La sidérurgie mondiale
Évolution de la répartition de la production mondiale :
|
Europe de l’Ouest |
Amérique du Nord |
ex URSS |
Japon |
Chine |
Autres pays |
1930 |
44,9 % |
43,8 % |
6,1 % |
2,4 % |
|
2,8 % |
1950 |
31,2 % |
46,7 % |
14,0 % |
2,5 % |
|
5,6 % |
1970 |
33,9 % |
21,9 % |
19,5 % |
15,7 % |
|
9,0 % |
1980 |
31,1 % |
16,4 % |
20,6 % |
15,5 % |
|
20,2 % |
1990 |
21,8 % |
13,1 % |
20,0 % |
14,3 % |
9 % |
21,8 % |
1995 |
22,8 % |
14,4 % |
10,5 % |
13,6 % |
12,7 % |
26,0 % |
2010 |
9,7 % |
6,7 % |
8,0 % |
7,1 % |
46,4 % |
22,0 % |
2015 |
8,8 % |
5,6 % |
6,2 % |
6,5 % |
49,6 % |
23,3 % |
2020 |
7 % |
4 % |
5 % |
4 % |
57 % |
23 % |
Source : IISI, Steel Statistical Yearbook
Importance de la Chine : devenue n°1 mondial, la progression importante de la production mondiale de ces dernières années est principalement due à la Chine et dans une moindre mesure à l’Inde. Importatrice d’acier jusqu’en 2004, en 2005, la Chine a équilibré importations et exportations (27,3 millions de t d’acier importées pour 27,4 millions de t exportées). En 2024 elle est exportatrice nette avec 108,4 millions de t. Ses besoins en matières premières (minerai de fer, nickel…) sont considérables et font de la Chine un acteur important sur les marchés de matières premières.
Importance du Japon : 2ème producteur mondial jusqu’en 2016, doublé depuis par l’Inde. Le développement de la sidérurgie japonaise est récent : après la 2ème guerre mondiale. La production a été multipliée par 12 de 1955 à 1973. Le Japon n’a ni charbon ni minerai de fer. Cette situation est caractéristique de la modification de l’implantation géographique de la sidérurgie. En France, déclin de la Lorraine au profit du littoral : Dunkerque en 1962, Fos en 1975. La sidérurgie de la Corée du Sud a suivi la même voie que celle du Japon. En 2024, les exportations nettes du Japon sont de 25,0 millions de t.
La sidérurgie américaine est moins performante que la sidérurgie européenne : les produits japonais mais aussi européens sont compétitifs sur le marché américain. Les États-Unis sont importateurs nets avec, en 2024, 18,6 millions de t.
Le commerce international de l’acier est important : 449 millions de t en 2024. Bien que les pays en voie de développement construisent des sidérurgies nationales (c’est un critère de développement) ils restent globalement importateurs.
Union européenne : en 2023, les exportations de l’Union Européenne ont porté sur 10,660 millions de t de produits plats et 5,614 millions de t de produits longs et les importations sur 20,116 millions de t de produits plats et 5,466 millions de t de produits longs.
Les exportations de produits plats sont destinés à 17 % à la Turquie, 15 % aux États-Unis, 7 % au Mexique, 6 % à la Suisse, 4 % à l’Égypte, celles de produits longs, à 12 % à la Suisse, 11 % aux États-Unis, 9 % à la Turquie, 7 % au Canada, 6 % au Mexique.
Les importations de produits plats proviennent à 13 % de Corée du Sud, 13 % d’Inde, 11 % de Taipei chinois, 10 % du Vietnam, 9 % du Japon, celles de produits longs, à 20 % de Turquie, à 8 % de Chine, 7 % d’Égypte, 7 % de Suisse, 5 % de Malaisie, 5 % d’Algérie.
Les principales sociétés sidérurgiques européennes sont regroupées dans Eurofer.
Évolution de la sidérurgie européenne entre 1978 et 1998 : nombre de hauts fourneaux : de 281 à 89, nombre de convertisseurs à oxygène : de 193 à 95, nombre de fours électriques : de 539 à 195.
Nombre d’employés dans l’Union européenne, en 2024 : 303 520 dont 79 500 en Allemagne.
Carte de la sidérurgie de l’Union européenne, en 2021 (document d’Eurofer) :
Utilisation mondiale des procédés de production : en 2024, en % de la production.
Pays |
Coulée continue |
Oxygène |
Électrique |
Martin |
Monde |
97,5 |
70,4 |
29,1 |
0,5 |
Union européenne |
97,4 |
55,6 |
44,4 |
0 |
France |
97,2 |
62,7 |
37,3 |
0 |
Allemagne |
97,7 |
70,9 |
29,1 |
0 |
Italie |
100 |
10,7 |
89,3 |
0 |
Japon |
99,1 |
73,8 |
26,2 |
0 |
États-Unis |
99,7 |
28,2 |
71,8 |
0 |
Russie |
83,8 |
63,6 |
34,2 |
2,2 |
Chine |
98,4 |
89,9 |
10,2 |
0 |
Source : Worldsteel, World steel in figures
Schéma simplifié de l’approvisionnement de la sidérurgie mondiale en millions de t de fer contenu, en 2019.
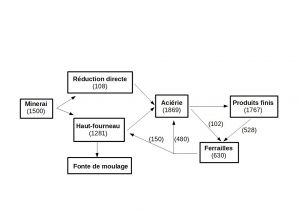
Principaux producteurs : en productions de 2024.
en millions de tonnes d’acier
China Baowu (Chine) |
130,1 |
|
Tata Group (Inde) |
31,0 |
ArcelorMittal (Luxembourg) |
65,0 |
|
Delong Steel (Chine) |
29,3 |
Ansteel Group (Chine) |
59,6 |
|
JSW Steel (Inde) |
26,9 |
Nippon Steel (Japon) |
43,6 |
|
Hunan Steel (Chine) |
24,9 |
HBIS (Chine) |
42,3 |
|
JFE Steel Corporation (Japon) |
23,5 |
Shagang Group (Chine) |
40,2 |
|
Jingye Group (Chine) |
22,7 |
Jianlong Group (Chine) |
39,4 |
|
Nucor Corporation (États-Unis) |
22,7 |
Posco (Corée du Sud) |
37,8 |
|
Shandong Steel Group (Chine) |
19,5 |
Shougang Group (Chine) |
31,6 |
|
Liuzhou Steel (Chine) |
19,2 |
Source : Worldsteel in figures
- China Baowu est issu de la fusion, en décembre 2016, des groupes chinois Baosteel et Wuhan Steel Group.
- A compter de 2006, après l’acquisition d’Arcelor par Mittal Steel, ArcelorMittal est devenu n°1 mondial jusqu’en 2019. Mittal avait dans un premier temps regroupé les activités des sociétés néerlandaises Ispat International et LNM Holding puis acquis ISG (International Steel Group). Arcelor était né en février 2002 de la fusion d’Usinor (France), Aceralia (Espagne) et Arbed (Luxembourg). Au préalable, Usinor avait repris, en 1998, le groupe belge Cockerill. En 2005, Arcelor avait absorbé le brésilien CST.
- Depuis octobre 2012, la fusion des groupes japonais Nippon Steel et Sumitomo est effective.
- JFE (Japan Fe Engineering) est né, en 2002, de la fusion de NKK et de Kawasaki Steel.
- En juin 2025, Nippon Steel a acquis le groupe américain US Steel.
Situation française
En 2022, en milliers de t d’acier.
Production : 12 100 d’acier brut (19 200 en 2007, 12 800 en 2008).
- Filière fonte : 8 155,
- Filière électrique : 3 945.
Consommation apparente : 13 800.
Commerce extérieur : en 2020, en milliers de t d’acier, hors aciers inoxydables, ferrailles et ferroalliages.
Exportations : 9 617 avec la répartition suivante :
Espagne |
29 % |
|
Belgique |
15 % |
Allemagne |
19 % |
|
Turquie |
7 % |
Italie |
15 % |
|
Royaume Uni |
7 % |
Source : ITC
Importations : 9 867 avec la répartition suivante :
Allemagne |
26 % |
|
Italie |
11 % |
Belgique |
23 % |
|
Pays Bas |
6 % |
Espagne |
14 % |
|
Luxembourg |
3 % |
Source : ITC
Effectifs : 25 317 personnes (150 000 en 1978).
Hauts fourneaux :
Destinés à élaborer de l’acier :
- 3 hauts fourneaux à Dunkerque (59), exploités par ArcelorMittal.
- 2 hauts fourneaux à Fos-sur-Mer (13), exploités par ArcelorMittal.
Destiné à élaborer de la fonte ductile :
- 1 haut fourneau à Pont-à-Mousson (54), exploité par Saint-Gobain PAM. L’introduction d’une faible quantité de magnésium dans la fonte grise permet de cristalliser le carbone sous forme de sphères de graphite au lieu de lamelles. Ce graphite sphéroïdal confère à la fonte une haute limite élastique et une grande résistance aux chocs. Elle est utilisée dans les canalisations, les regards de chaussée pour la voirie…
Aciéries électriques : en France fonctionnent 20 aciéries électriques.
Utilisations
Consommations apparentes finales d’acier
En 2024. Monde : 1 742,4 millions de t et 214,7 kg/habitant/an, Union européenne : 130,1 millions de t et 290,7 kg/habitant/an.
en millions de t et ( ) en kg/habitant/an
Chine |
857 (601) |
|
Russie |
44 (304) |
Inde |
148 (103) |
|
Turquie |
38 (444) |
États-Unis |
89 (261) |
|
Mexique |
28 (213) |
Japon |
51 (419) |
|
Allemagne |
26 (313) |
Corée du Sud |
48 (923) |
|
Brésil |
26 (119) |
Source : Worldsteel, World steel in figures
La consommation par habitant la plus importante, en 2018, est celle des Émirats Arabes Unis avec 941 kg/habitant/an, suivie de la Corée du Sud avec 807 kg/habitant/an, de Chypre avec 665 kg/habitant/an, de Taipei chinois avec 613 kg/habitant/an, du Canada avec 549 kg/habitant/an. Celle de la République Démocratique du Congo est de 1,4 kg/habitant/an.
Secteurs d’utilisation de l’acier
En 2024, dans le monde. Source : Worldsteel Association
Secteurs d’utilisation de l’acier : en 2024, dans le monde.
Construction et infrastructures |
52 % |
|
Autres transports |
5 % |
Équipements mécaniques |
16 % |
|
Équipements électriques |
3 % |
Automobiles |
12 % |
|
Appareils ménagers |
2 % |
Fabrication d’objets métalliques |
10 % |
|
|
|
Source : Worldsteel Association
Dans l’Union européenne, en 2023, la construction représente 35,5 % des utilisations, l’automobile 19,1 %, les équipements mécaniques et électriques 14,7 %, la fabrication d’objets métalliques 14,4 %, les tubes 9,3 %, les appareils ménagers 2,3 %, les autres transports 2,8 %.
Le bâtiment et les travaux publics utilisent principalement des produits longs (poutrelles, ronds à béton…), l’automobile, par contre, utilise plutôt des produits plats (tôles…).
Les aciers spéciaux
Parmi les très nombreuses variétés d’aciers, on peut citer :
- Les aciers inoxydables : contenant par exemple 18 % de Cr et 10 % de Ni pour les aciers austénitiques. En 2021, production de 58,289 millions de t dans le monde dont 270 000 t, en France. Pour plus de détails sur les aciers inoxydables voir ce chapitre.
- Les aciers à roulements : contenant 1 % de C, 1,5 % de Cr.
- Les aciers à outils : contenant jusqu’à 18 % de W, 1,5 % de C.
- D’autres aciers alliés spéciaux : tôles pour transformateurs (3 % de Si), aciers à ressort (Mn-Si ou Cr-Mo-Si), aciers pour cryogénie (6 à 9 % de Ni), aciers pour chaudières (Mn-Mo ou Cr-Mo), aciers résistant à l’abrasion (13 % de Mn), aciers à dilatation nulle (Invar, 36 % de Ni), aciers magnétiques (Fe-Al-Ni), aciers réfractaires (25 % de Cr, 12 % de Ni).
Utilisations particulières
Les tôles sandwich : elles sont constituées par 2 tôles minces (0,3 à 0,7 mm) séparées par un film polymère de 45 micromètres. La résine est appliquée sur l’une des tôles puis l’ensemble est colaminé. Plus légères et résistantes que l’acier d’épaisseur équivalente, elles sont utilisées pour leurs propriétés d’insonorisation : les vibrations sont absorbées par le polymère (choisi pour que la température d’utilisation soit dans son domaine viscoélastique), par frottement des chaînes polymères, qui dissipe cette énergie sous forme de chaleur. Ces tôles, mises au point initialement au Japon, commencent à être utilisées dans les tabliers (pièce séparant le moteur de l’habitacle) des automobiles (gain de poids : 20 %), les tambours de sèche linge… Le dallage du sol de la Très Grande Bibliothèque a été réalisé en sandwich d’acier inoxydable.
Bâtiment, travaux publics : en France, la consommation dans ce secteur est de 4 millions de t/an dont 44 % de ronds à béton. Les constructions métalliques utilisent 700 000 t/an, dont 40 000 t/an pour les ponts métalliques. La construction du viaduc de Millau a consommé 62 550 t d’aciers. Le pont le plus long au monde (4 km), celui de Akashi-Kaikyo, au Japon, a utilisé 193 000 t d’acier.
Dans ce secteur, les consommations annuelles par habitant sont de 268 kg au Japon, 151 kg en Italie, 118 kg en Allemagne, 108 kg aux États-Unis, 108 kg en Espagne, 83 kg en France. Les normes antisismiques conduisent à employer plus d’acier dans les constructions, au Japon et en Italie (de 46 à 48 % des utilisation de l’acier dans ces pays). On assiste au développement de la construction de maisons individuelles à ossature en acier.
Automobiles : elles renferment, en moyenne, 960 kg d’acier contenu à 34 % dans la structure du véhicule, 23 % dans le moteur, 12 % dans les suspensions. De nouvelles nuances d’aciers, à hautes limites élastiques (la limite d’élasticité est passée de 200 à 1000 et jusqu’à 1400 MPa), AHSS (Advanced High Strentgh Steel ou dual phase), UHSS (Ultra High Strength Steel ou martensitique) sont de plus en plus utilisées.
Tubes : le producteur français Vallourec est le n°1 mondial des tubes sans soudure, laminés à chaud ou à froid. Ses capacités de production sont de 3 millions de t/an.
Rails : 400 km de ligne de TGV à 2 voies nécessitent 100 000 t de rail (60 kg/m). En France, une seule usine de production de rails à partir d’acier importé du Royaume-Uni, à Hayange (57). Depuis 2021, l’usine est contrôlée par le groupe Saarstahl. Les rails produits d’une longueur de 80 m (en 2017, les rails atteignent jusqu’à 150 m) étaient, pour la construction de la ligne TGV Est, soudés par la SNCF pour atteindre 400 m. La première phase de la construction de cette ligne, qui a débuté en 2002, a consommé 86 000 t de rails. Actuellement les rails produits ont une longueur de 108 m et la capacité de production est de 350 000 t/an. Dans le monde, la longueur du réseau ferré est de 1,052 million de km.
Signalisation routière : 200 000 t d’acier/an en Europe de l’Ouest.
Boules de pétanque : la société française Obut, à Saint-Bonnet-le-Château (42), en produit 300 t/mois, soit les 2/3 du marché mondial. Les boules sont fabriquées à partir de barres cylindriques cisaillées, forgées à plus de 1000°C pour donner des flans qui sont emboutis en coquilles soudées 2 à 2 qui subissent diverses finitions et traitements thermiques.
Bibliographie
- Alliance des Minerais, Minéraux et Métaux (A3M), 17 rue de l’Amiral Hamelin, 75783 Paris Cedex 16.
- Statistiques et site Internet de Worldsteel Association, Rue Colonel Bourg, 120, B-1140 Bruxelles, Belgique.
- « Western Australia iron ore industry profile« , Government of Western Australia, Août 2017.
- Midrex Technologies, 3735 Glen Lake Drive, Suite 400, Charlotte, Caroline du Nord, 28208 États-Unis.
- The White book of steel, World Steel Association, 2012.
- Le Livre de l’Acier, Technique & Documentation – Lavoisier, 1994.
- Bureau of International Recycling (BIR), Av. F. Roosevelt, 24, B-1050 Bruxelles, Belgique.
- Site Internet d’Eurofer, European Confederation of Iron and Steel Industries, Av de Cortenbergh, 172, B-1000 Bruxelles, Belgique.
- Revue de Métallurgie, nombreux numéros.
Archives
Aciers 2023
Aciers 2022
Aciers 2019
Aciers 2015
Aciers 2013
Aciers 2012
Aciers 1996
Aciers 1993
Commentaires récents