Données physico-chimiques
Données atomiques
Formule |
Masse molaire |
Minéral |
Structure cristalline |
Na2SO4 |
142,04 g.mol-1 |
thénardite |
orthorhombique de paramètres a = 0,975 nm, b = 1,229 nm et c = 0,285 nm |
Données physiques
Masse volumique |
Température de fusion |
Solubilité dans l’eau |
2,68 g.cm-3 |
884°C |
- à 0°C : 4,76 g/100 g d’eau
- à 100°C : 42,7 g/100 g d’eau
|
Données thermodynamiques
Sulfate de sodium cristallisé :
- Enthalpie molaire standard de formation à 298,15 K : -1 385 kJ.mol-1
- Enthalpie libre molaire standard de formation à 298,15 K : -1 267,3 kJ.mol-1
- Entropie molaire standard à 298,15 K : S° = 149,5 J.K-1mol-1
- Capacité thermique molaire sous pression constante à 298,15 K : Cp° = 127,7 J.K-1mol-1
- Enthalpie molaire standard de fusion à la température de fusion : 24,3 kJ.mol-1
Données industrielles
Le sulfate de sodium, appelé également sel de Glauber (Na2SO4,10H2O) lorsqu’il est hydraté, est soit extrait de dépôts naturels (Chine, Canada, États-Unis, Espagne, Turquie, Russie…), soit fabriqué industriellement. Dans ce cas il est obtenu directement par synthèse ou récupéré comme sous-produit lors de diverses fabrications chimiques (viscose, acide borique, acide ascorbique, résorcine, cellulose, pigments de silice, dichromate de sodium, méthionine…) ou encore lors du traitement des batteries usagées. En 2020, le sulfate naturel représente environ 70 % de la production mondiale.
État naturel
Le sulfate de sodium, comme le carbonate de sodium ou le chlorure de sodium, est un sel soluble dans l’eau qui ne peut se rencontrer, à l’état solide, que lorsque certaines conditions sont réunies et, en particulier, un climat aride qui permet la concentration du sel dans des mers fermées ou des lacs et sa précipitation. Ce processus est en cours actuellement, ou s’est produit au cours des temps géologiques dans des dépôts fossiles.
Dépôts naturels de sulfate de sodium
Minerais : les principaux sont la thénardite (Na2SO4), la mirabilite ou sel de Glauber (Na2SO4,10H2O), la glaubertite (Na2SO4,CaSO4), la glaserite (Na2SO4,3K2SO4).
Gisements canadiens : ils sont exploités dans la province du Saskatchewan.
- La société Saskatchewan Mining and Minerals exploite des saumures et des couches de sel à Chaplin depuis 1948 et Ingebrigt depuis 1966 avec au total une capacité de production de 285 000 t/an. Les saumures sont déversées dans des étangs d’évaporation où les sels dissous se concentrent puis, en automne, la baisse des températures permet la précipitation du sulfate de sodium. En 2018, après 70 ans d’exploitation, la production a atteint un total de 11 millions de t.
- Les saumures du lac Whiteshore, sont exploitées à Palo, par la société Nanostructured Minerals Corporation, avec une capacité de production de 100 000 t/an.
Gisements des États-Unis : le sulfate de sodium est extrait de saumures.
- A Westend en Californie, du sulfate de sodium est récupéré avec une capacité de production de 200 000 t/an, ainsi que du borax et du carbonate de sodium, lors du traitement des saumures du lac Searles, exploitées par la société Searles Valley Minerals, filiale du groupe indien Nirma (voir les chapitres consacrés à ces produits). Les réserves sont de 450 millions de t. Le sulfate de sodium représente 35 % des sels en solution.
- A Brownfield et Seagraves, au Texas, avec une capacité de production de 150 000 t/an, les saumures sont exploitées par Cooper Natural Resources (CNR).
Gisement mexicain : la saumure de la Laguna del Rey, dans l’état de Coahuila, est exploitée à Quirey par la société Quimica del Rey, filiale du groupe Industrias Peñoles, avec une capacité de production de 780 000 t/an. En 2023, la production a été de 699 316 t.
Gisements espagnols : se sont des dépôts fossiles.
- L’ « Unitad salina » située dans le bassin sédimentaire de Madrid est exploitée dans les mines de Sulquisa près de Villaconejos et d’El Castellar près de Villarrubia de Santiago.
- Mine de Sulquisa : le gisement de glaubertite est situé sous environ 20 m de stérile. Il est exploité à l’aide de la méthode des étangs de dissolution. Cette méthode consiste à décaper la couche stérile puis à dissoudre la glaubertite, fracturée par des explosifs, dans des saumures de retour de l’usine de récupération du sulfate de sodium. Na2SO4,10H2O précipite par refroidissement et est séparé à l’aide d’hydrocyclones. Avec une capacité de production de 300 000 t/an, la mine est exploitée par la société Sulquisa, appartenant au groupe espagnol Minersa.
- Mine d’El Castellar : le gisement de thénardite, avec une teneur de 62 à 65 %, et de glaubertite qui se présente sous forme d’une couche de 5 à 8 m d’épaisseur est exploité à l’aide de techniques minières classiques des exploitations souterraines (méthode des chambres et piliers). Le minerai, après concassage, est dissous puis le sulfate cristallise par évaporation. Les réserves sont estimées à 10 millions de t. Avec une capacité de production de 300 000 t/an, la mine est exploitée par la société Minera de Santa Marta (MSM), filiale du groupe SAMCA.
- Le gisement de Cerezo de Río Tirón est situé près de Burgos, dans le bassin de l’Ebre. Une couche de 8 m de glaubertite, avec une teneur de 32 à 40 %, est exploitée à ciel ouvert par la méthode des étangs de dissolution.
- Il est exploité, avec plus de 700 000 t/an et des réserves de plus de 350 millions de t, par la Compañia Minera Río Tirón, filiale du Grupo Crimidesa.
- La société Minera de Santa Marta exploite également ce dépôt, à Belorado avec 340 000 t/an.
Gisements turcs : le sulfate de sodium est extrait de lacs salés ou de dépôts fossiles, principalement par la société Alkim Alkali Kimya, qui possède une capacité de production 470 000 t/an. En 2023, la production a été de 354 959 t. La production est issue de l’exploitation des saumures du lac Acigol dans l’usine de Koralkim, avec une capacité de production de 130 000 t/an, de celles des lacs de Tersakan et Bolluk dans l’usine de Konya-Cihanbeyli, avec une capacité de 80 000 t/an et du gisement souterrain de Çayirhan, avec une capacité de 210 000 t/an qui devrait être portée à 390 000 t/an. Les réserves du gisement de Çayirhan sont de 196 millions de t de glaubertite renfermant 65 millions de t de sulfate de sodium.
Gisement russe : situées dans la région de l’Altaï, les saumures du lac Kuchuk qui contiennent 7 % de sulfate de sodium, sont exploitées par la société Kuchuksulphate. Elles sont pompées dans des étangs de cristallisation où, lorsque la température est inférieure à 5°C, la mirabilite cristallise. La production, en 2023, est de 383 000 t.
Productions de sulfate naturel
Dans le monde, environ 8 millions de t/an.
Principaux pays producteurs : Chine, Espagne, Mexique, Turquie, Russie, Canada, États-Unis, Argentine, Chili…
En Chine, le principal producteur, n°1 mondial, est NaFine Chemical Industry Group, qui exploite, en particulier, dans la province du Shanxi, le lac salé de Yuncheng. La production du groupe représente 30 % de la production chinoise. Par ailleurs, Jiangsu Yinzhu Chemical possède une capacité de production de 2 millions de t/an et Xinli Chemicals possède une capacité de production de 1,6 million de t/an avec 3 unités de production : Hengyang, Lixian et Xinjin.
En 2021, la production espagnole a été de 1,562 million de t de sulfate de sodium contenu dont 1,278 million de t dans de la glaubertite et 284 000 t dans de la thénardite. Les exportations ont porté, en 2019, sur 1,518 million de t, destinées à 40 % au Brésil, 7 % au Royaume Uni, 5,5 % au Maroc… L’Espagne est le seul pays producteur de sulfate de sodium naturel de l’Union européenne.
Réserves : les réserves mondiales sont estimées, en 2013, à 3,3 milliards de t :
en millions de t
États-Unis |
860 |
|
Turquie |
100 |
Espagne |
180 |
|
Canada |
84 |
Mexique |
170 |
|
|
|
Source : USGS
Des ressources identifiées sont présentes dans les autres pays suivants : Botswana, Égypte, Italie, Mongolie, Roumanie, Afrique du Sud.
Aux États-Unis, dans le Grand Lac Salé de l’Utah, actuellement non exploité pour le sulfate de sodium contenu, ce dernier représente 12 % des sels contenus. Ses réserves sont de 400 millions de t.
Fabrication industrielle du sulfate de sodium synthétique
Synthèse directe
Il peut être préparé par synthèse directe, selon le procédé Mannheim. La réaction, mise en œuvre dans des fours à moufle, à 500-600°C, est la suivante :
2 NaCl + H2SO4 = Na2SO4 + 2 HCl
Co-productions
Mais il est surtout co-produit lors de diverses fabrications : fibres de viscose (rayonne), acide borique, pâte à papier, carbonate de lithium, méthionine, dichromate de sodium, vitamine C, caprolactame, uranium, épuration des fumées…
L’acide borique (H3BO3 ou acide orthoborique), par exemple, est préparé par attaque sulfurique du borax en donnant également du sulfate de sodium :
Na2B4O7,10H2O + H2SO4 = 4 H3BO3 + Na2SO4 + 5 H2O
Le dichromate de sodium (Na2Cr2O7) est préparé à partir du chromate de sodium selon la réaction suivante :
2 NaCrO4 + H2SO4 = Na2Cr2O7 + Na2SO4 + H2O
L’acide sulfurique des batteries usagées, autre exemple, est neutralisé par de l’hydroxyde de sodium pour donner du sulfate de sodium, récupéré par évaporation de la solution, selon la réaction :
2 NaOH + H2SO4 = Na2SO4 + 2 H2O
Dans l’Union européenne, sauf en Espagne, la production est uniquement synthétique, les principales co-productions étant lors de la fabrication de la viscose et de la méthionine.
Co-production de Na2SO4 lors de la fabrication de fibres de viscose
Les fibres de viscose sont des fibres artificielles obtenues à partir de la cellulose du bois. Les fibres continues sont appelées rayonne, les fibres discontinues fibranne.
La pulpe de cellulose, est hydrolysée dans une solution d’hydroxyde de sodium, à la température ambiante, selon la réaction :
(C6H10O5)n + n NaOH = (C6H9O4ONa)n + n H2O
Après pressage pour éliminer une grande partie de l’eau, la pulpe est déchiquetée puis laissée en présence du dioxygène de l’air à une température comprise entre 18 et 30°C afin de réduire le degré de polymérisation, le poids moléculaire diminuant d’un facteur 2 à 3. Afin de rendre soluble l’alcali-cellulose formée, on lui fait subir une xanthatation à l’aide de disulfure de carbone selon la réaction suivante :
(C6H9O4ONa)n + n CS2 = (C6H9O4O-SC-SNa)n
Dans une solution diluée d’hydroxyde de sodium, le xanthate de cellulose qui a pris une couleur jaune orangée, passe en solution ou plutôt en fine suspension visqueuse d’où le nom de viscose.
Après une durée de mûrissement, qui achève la mise en solution de la viscose, une filtration pour éliminer les impuretés insolubles et une désaération, la viscose est extrudée à travers une filière puis plonge dans une solution d’acide sulfurique en présence de sulfate de sodium et de sulfate de zinc, où la cellulose est régénérée et précipite selon la réaction :
(C6H9O4O-SC-SNa)n + n/2 H2SO4 = (C6H10O5)n + n CS2 + n/2 Na2SO4
Ainsi, la production d’une tonne de viscose, donne une co-production de 0,438 t de sulfate de sodium.
Ce procédé classique de production utilisant du disulfure de carbone, produit toxique, de nouveaux procédés se sont développés, en particulier le procédé Lyocell, qui utilise un solvant de la cellulose, la N-méthylmorpholine (NMMO). Toutefois le procédé classique reste nettement le plus employé. La consommation mondiale de viscose représente, en 2018, 6,3 % d’un total de 106 millions t de fibres dont 62,5 % de fibres synthétiques, 25,3 % de fibres de coton et 1,1 % de fibres de laine.
Principaux producteurs de viscose :
- Lenzing, groupe autrichien, qui possède selon le procédé classique une capacité de production de 785 000 t/an de viscose dont 284 000 t/an à Lenzing, en Autriche, 323 000 t/an à Purwakarta, en Indonésie et 178 000 t/an à Nanjing, en Chine. Par ailleurs Lenzing possède une capacité de production de 260 000 t/an selon le procédé Lyocell, à Mobile, dans l’Alabama, aux États-Unis, avec 51 000 t/an et en Europe, en Autriche à Lenzing avec 74 000 t/an et Heiligenkreuz avec 90 000 t/an et au Royaume Uni à Grimsby avec 45 000 t/an. Construit une usine à Prachinburi, en Thaïlande d’une capacité de 100 000 t/an, prévue fin 2021, selon le procédé Lyocell.
- Les groupes chinois, Fulida et Tangshan Sanyou ont chacun une capacité de production de 500 000 t/an.
- Grassim, société du groupe indien Aditya Birla, possède une capacité de production de 788 000 t/an, en Inde, à Nagda dans le Madhya Pradesh, Kharach et Vilayar, dans le Gujurat, Harihar, dans le Karnataka et en Chine, à Birla Jingwei à travers une joint-venture. En 2022-23, la production a été de 711 000 t.
Co-production de Na2SO4 lors de la fabrication de la méthionine
La méthionine est un acide aminé essentiel non synthétisé par l’homme ou les animaux, présent, en faible quantité, dans les céréales. La synthèse chimique donne de la méthionine racémique (renfermant à parts égales les énantiomères lévogyres et dextrogyres). Par contre la méthionine obtenue par biotechnologie donne seulement la forme lévogyre. Les animaux ne peuvent convertir que la forme lévogyre en protéines. La formule de la méthionine ou acide 2-amino-4-méthylthio butyrique est la suivante :
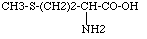
Le procédé chimique développé par Adisseo pour la production de méthionine en poudre utilisée en alimentation animale s’effectue en 3 étapes :
- Synthèse de l’hydantoïne : par action du cyanure de sodium, en présence d’ammoniac et de dioxyde de carbone, sur l’aldéhyde méthylthiopropionique (AMTP), lui même obtenu par réaction entre le méthyl mercaptan et l’acroléine.
- Hydrolyse de l’hydantoïne dans la solution formée lors de la première étape, par de l’hydroxyde de sodium, en présence du carbonate de sodium de la solution : on obtient le méthioninate de sodium :
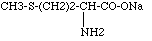
- Formation de la méthionine par neutralisation à l’aide d’acide sulfurique :
méthioninate + Na2CO3 + 3/2 H2SO4 = méthionine + 3/2 Na2SO4 + CO2
La production de sulfate de sodium est de l’ordre de 1,3 t/t de méthionine.
Principaux producteurs de méthionine : en 2020, sur un total mondial de 1,900 million de t/an.
Sources : Adisseo et rapports des sociétés
- Evonik (Allemagne), n°1 mondial, produit de la méthionine à Anvers, en Belgique, avec 260 000 t/an, à Mobile, dans l’Alabama, aux États-Unis, à Wesseling, en Allemagne et Singapour, avec 300 000 t/an.
- Adisseo, société du groupe chinois Blue Star, produit de la méthionine, en France à Roussillon (38) et à Commentry (03), en Espagne à Burgos et en Chine à Nanjing, avec 350 000 t/an.
- Novus, société commune aux groupes japonais Mitsui avec 80 % des parts et Nippon Soda avec 20 %, possède, aux États-Unis à Chocolate Bayou, au Texas, une capacité de production de méthionine de 255 000 t/an.
- Sumitomo Chemical (Japon) possède une capacité de production de 250 000 t/an à Niihama, dans la préfecture de Ehime.
- CJ Cheiljedang (Corée du Sud) s’est associé au groupe français Arkema, qui fournit le méthyl mercaptan, pour construire une usine de production de L-méthionine par biofermentation à Kerteh, en Malaisie, avec une capacité de production de 80 000 t/an depuis 2015.
Le principal débouché de la méthionine (à 90 %) est l’alimentation de la volaille (2 à 3 g/kg d’aliment, soit au total 4 à 5 g par poulet). La consommation mondiale est de 1,6 million de t en 2022.
Productions de sulfate naturel et synthétique
En 2020, la production mondiale est de 24 millions de t. Elle est à 70 % à partir de sulfate naturel.
La Chine, en particulier dans la province de Jiangsu, est le principal pays producteur avec 79 % de la production mondiale.
Autres pays producteurs : l’Espagne avec 1,562 million de t, en 2021, les États-Unis avec 475 000 t (environ moitié-moitié entre naturel et synthétique), en 2018.
En Europe, Turquie comprise, le sulfate naturel représente 61 % de la production, le sulfate synthétique coproduit lors de la fabrication de viscose, 22 %, les autres coproductions, 17 %.
Commerce international : en 2024.
Principaux pays exportateurs sur un total de 6,055 millions de t, en 2023.
en milliers de t
Chine |
4 473 |
|
Turquie |
111 |
Espagne, en 2023 |
936 |
|
Indonésie |
79 |
Inde |
288 |
|
Canada |
78 |
États-Unis |
223 |
|
France |
50 |
Source : ITC
Les exportations chinoises sont destinées à 14 % au Bangladesh, 10 % au Vietnam, 9 % au Brésil, 8 % à l’Indonésie.
Principaux pays importateurs.
en milliers de t
Brésil |
856 |
|
Nigeria |
261 |
Bangladesh |
738 |
|
Thaïlande |
257 |
Vietnam |
443 |
|
Tanzanie |
191 |
Indonésie |
338 |
|
Philippines |
187 |
Colombie |
305 |
|
Guatemala |
158 |
Source : ITC
Les importations du Brésil proviennent à 52 % d’Espagne, 47 % de Chine.
Principaux producteurs dans l’Union européenne, en capacités de production.
Sulfate naturel : producteurs espagnols.
Sources : sites des sociétés
Sulfate synthétique :
Lenzing (Autriche, 200 000 t/an à Lenzing), Cordenka (Allemagne, 40 000 t/an à Obernburg) : fabricants de viscose.
Adisseo (France et Espagne), Evonik (Allemagne et Belgique) : fabricants de méthionine.
Situation française
En 2024.
Producteur :
Adisseo possède une capacité de production de 90 000 t/an, provenant de la fabrication de la méthionine. Les usines sont situées à Roussillon (38) et Commentry (03).
Commerce extérieur :
Les exportations étaient de 49 129 t avec comme principaux marchés à :
- 35 % le Brésil,
- 8 % la Colombie,
- 7 % le Maroc,
- 6 % l’Italie.
Les importations s’élevaient à 45 234 t en provenance principalement à :
- 57 % d’Espagne,
- 16 % de Belgique,
- 10 % d’Allemagne,
- 7 % d’Autriche.
Utilisations
Consommation : en 2017, la consommation mondiale est de 15,90 millions de t, effectuée, en 2020, à 46 % en Chine continentale, 14 % en Amérique Centrale et du Sud, 12 % dans les autres pays asiatiques, 10 % en Amérique du Nord, 6 % en Europe de l’Ouest.
Secteurs d’utilisation : aux États-Unis, en 2012.
Détergents |
35 % |
|
Nettoyage des moquettes |
4 % |
Verre |
18 % |
|
Textiles |
4 % |
Pâte à papier |
15 % |
|
|
|
Sources : USGS
- Détergents : les lessives en poudre classiques contiennent de 16 à 45 % de Na2SO4, mais seulement de 4 à 5 % pour les poudres compactes. La diminution de la teneur en sulfate de sodium est à l’origine de ces dernières. Dans les lessives en poudre, le sulfate de sodium joue le rôle de fluidifiant et d’antimottant. Par ailleurs, les lessives liquides ne contiennent pas de sulfate de sodium. En 2016, dans le monde, les détergents représentent 39 % de la consommation de sulfate de sodium.
- Industrie du verre : le sulfate de sodium se décompose, vers 1200°C selon la réaction :
Na2SO4 = Na2O + SO2 + 1/2 O2
Le dégagement gazeux produit par cette décomposition, qui a lieu à une température plus élevée que celle du carbonate de sodium, facilite l’affinage du verre. Le sulfate de sodium est introduit à des teneurs inférieures à 1 %, en fin d’affinage.
- Industrie de la pâte à papier : le sulfate de sodium est réduit à l’aide de charbon en sulfure de sodium selon la réaction suivante :
Na2SO4 + 2 C = Na2S + 2 CO2
Cette production de sulfure de sodium utilisé dans le procédé kraft, est principalement réalisée en Chine.
Bibliographie
- Les carbonates et sulfates de sodium, Mémento du BRGM, décembre 1992.
- Panorama Minero, Instituto Geológico y Minero de España, Rios Rosas, 23, 28003 Madrid, Espagne.
- T. Willke, « Methionine production – a critical review« , Applied Microbiology and Biotechnology, 98, p 9894-9914; décembre 2014.
- Sodium Sulphate producers Association, CEFIC, Avenue E. van Nieuwenhuyse, 4 box 1, 1160 Bruxelles, Belgique.
Archives
Sulfate de sodium 2023
Sulfate de sodium 2022
Sulfate de sodium 2019
Sulfate de sodium 2015
Sulfate de sodium 2013
Sulfate de sodium 2011
Sulfate de sodium 1993
Commentaires récents